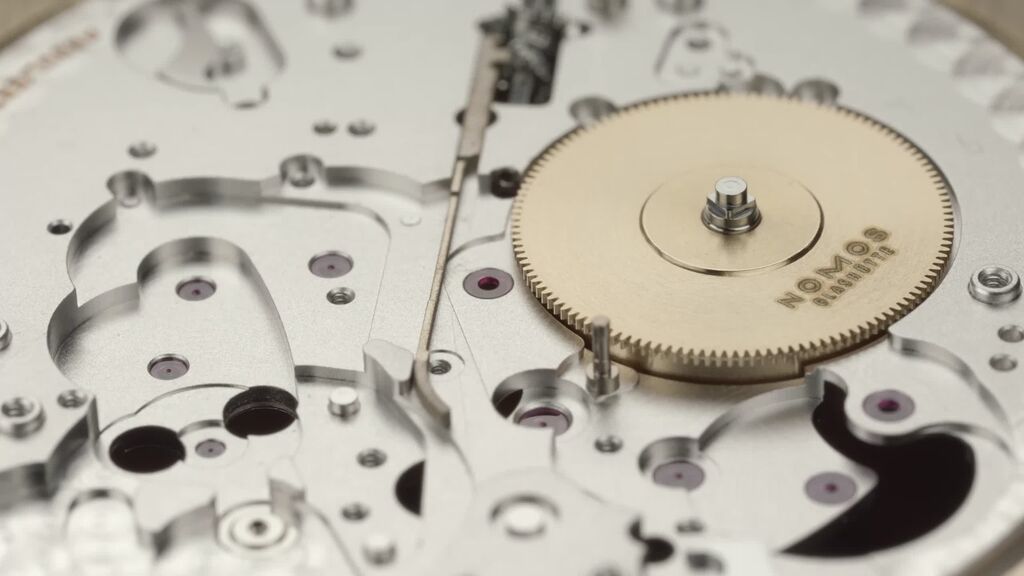
7.1. Assembling the gear train
The gear train: an umbrella term for numerous interlocking wheels. The DUW 3001 caliber provides an example of a running gear that transfers the power of the mainspring from the barrel—via the center wheel, third wheel, and second wheel—to the escape wheel. Another example is the automatic running gear, which uses the motions of the rotor to wind the mainspring. The number of turns of the individual wheels is progressively increased from the mainspring barrel to the escape wheel. After the first revolution of the barrel, the escape wheel has already rotated approximately 4,000 times. The automatic running gear works in exactly the opposite way. Here, the numerous motions of the rotor are converted into ever slower rotations. And everything happens under the Glashütte three-quarter plate, all on a single level. A thin and elegant design, which is a distinguishing feature of NOMOS watches.
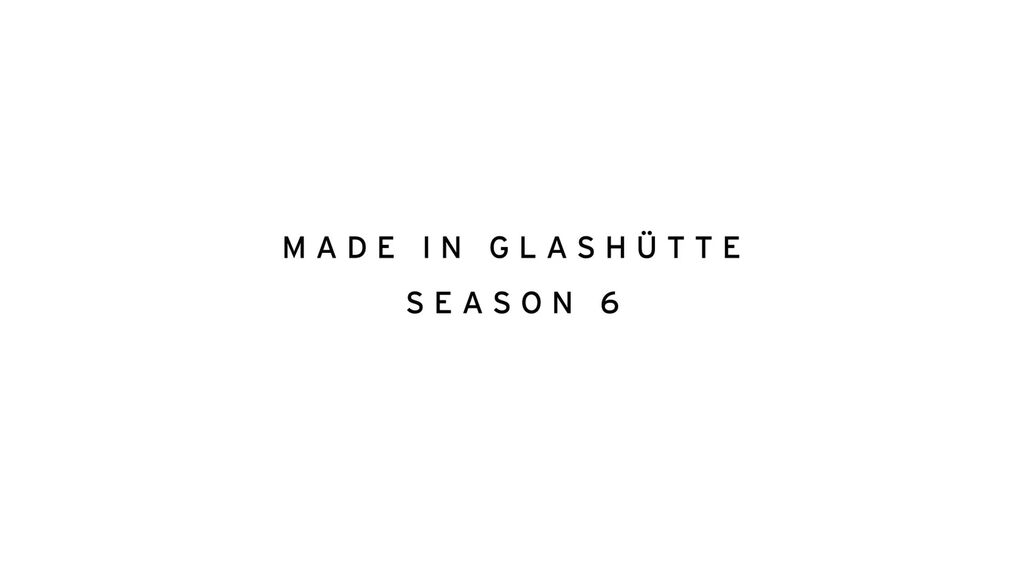
Precision in every detail
Quality is not something that is achieved by chance—but rather by methodical measuring, adjusting, fixing, checking, and testing, until everything sits just right and works as it should. Above all, it is the result of upholding the highest standards. To ensure that our mechanical timepieces meet these standards, precision is a priority in every work step. From the perfectly smooth surface of the baseplate to the careful assembly and adjustment of individual caliber components, right up to the selection of the most suitable strap; expertise and the correct production methods are combined with a clear vision to yield the best results. This collection of artistic short films introduces you to some of the many processes that go into creating a high precision timepiece from NOMOS Glashütte.
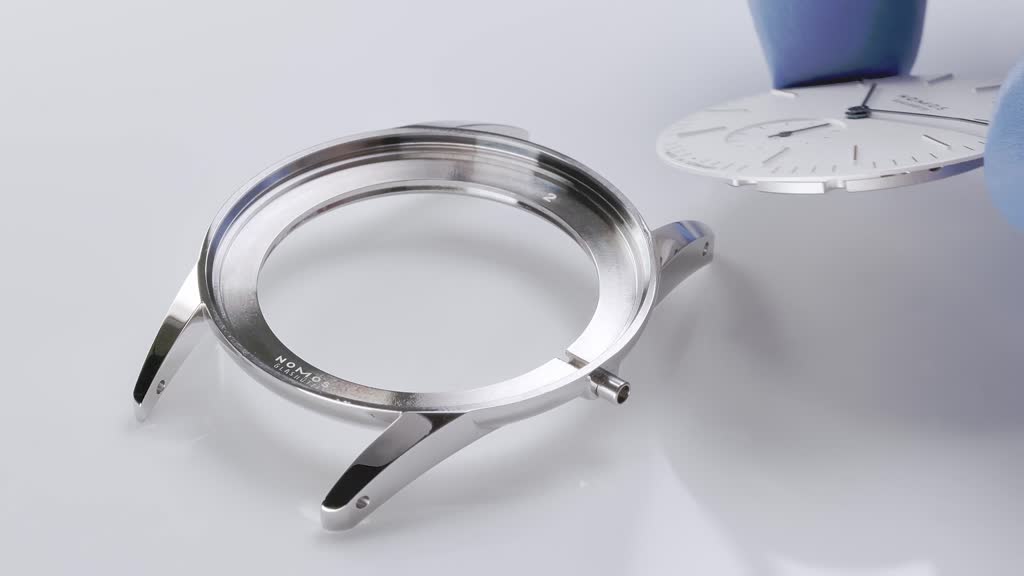
6.12. Encasing the movement
The movement, including the dial and hands, is on its final stage before reaching its destination—the case. The long journey of manufacturing and assembling a NOMOS watch is finally coming to an end; the movement is being encased. The precise mechanics, which have been assembled and adjusted in many hours of manual work, are now protected in the case, completing the design of this small masterpiece of craftmanship. The case, dial, and hands are combined to match the character of the respective NOMOS model. The sapphire crystal glass back provides a breathtaking view of the microcosm inside. But the final step still involves many stages. A final inspection lasting several days is dedicated to checking the accuracy, appearance, rate, water resistance, and numerous other aspects of the watch. Like a final exam, it is always exciting—and always gratifying when a watch passes with flying colors.
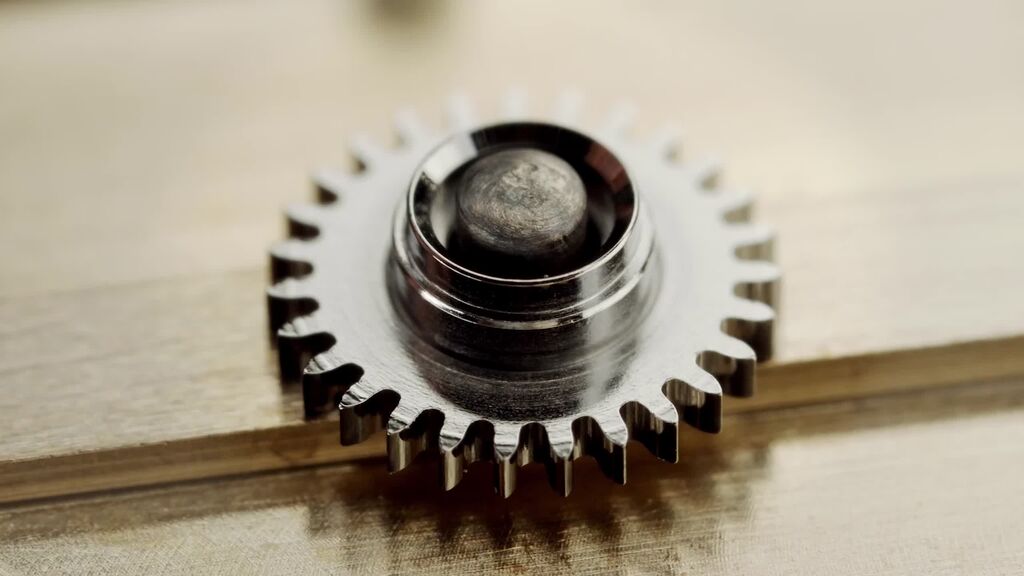
6.11. Pre-assembly of the corrector wheel
The corrector wheel is used in the neomatik caliber DUW 6101 for quick date adjustment. It allows the date to be adjusted in both directions (forward and backward) and prevents damage to the movement if an attempt is made to adjust the date manually during the short 90-minute locking period at midnight. Since the movement automatically switches to the next day at this point, manual correction is temporarily impossible. And if someone does try, the correction wheel gives way. Very clever! It has a slip clutch that engages at a certain force, allowing the gear driven by the crown to turn while the wheel remains stationary. The wheel and gear are riveted together with a friction spring. To ensure that the slip clutch does not engage too early or too late, everything must be perfectly coordinated, just like in a good team. We are happy to prove this and check every single correction wheel for the correct torque. Better safe than sorry!
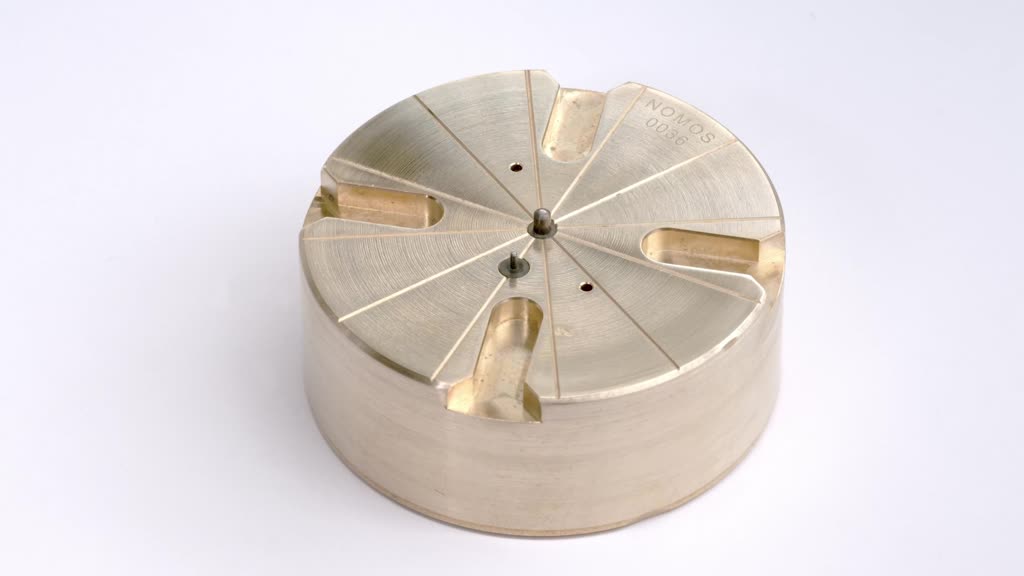
6.10. Visual inspection of the minute markers
The dial of a watch is like a face—it has character. It is the part of the watch that attracts the most attention, that everyone likes to look at, and which also tells us the time. Always in harmony with the hands. That's why we check every dial to ensure it is flawless, that the fine lines of the minute track are correctly positioned, that the base color harmonizes with the hands, and that the precise time information is a visual delight. Practicality in its most beautiful form.
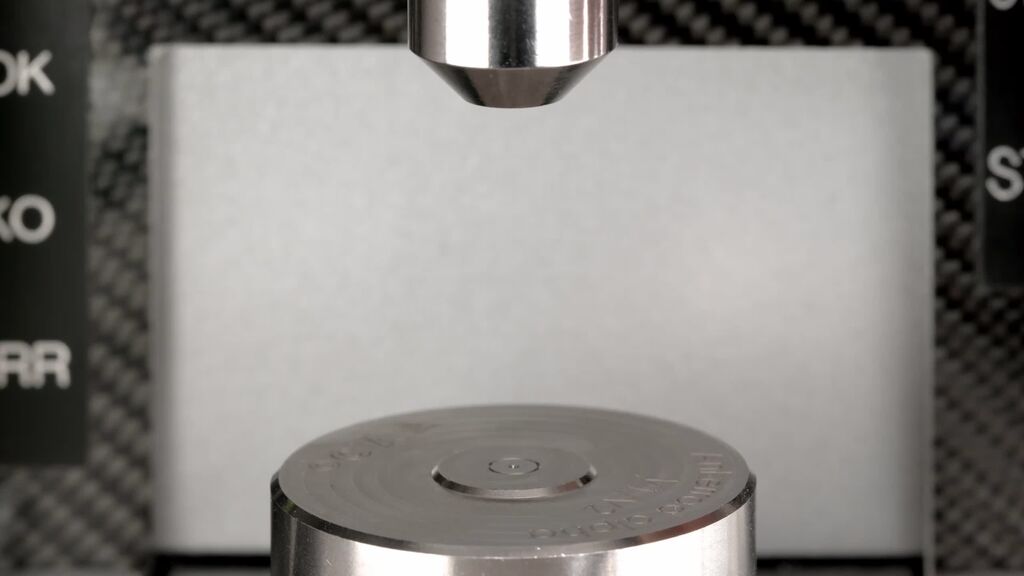
6.9. Testing the holding torque
The escape wheel, consisting of this single wheel and the escape wheel pinion, is riveted together at NOMOS Glashütte. The pinion receives power from the fourth wheel (which receives it from the mainspring), and the escape wheel transfers the power to the anchor. Of course, this only happens when the escape wheel and escape wheel pinion are firmly connected. At NOMOS, this is checked by trying to twist the wheel and pinion against each other—up to a defined force: the holding torque. Any actual twisting is immediately detected by the testing device. All wheels at NOMOS are checked this way. After all, only stable assembly processes lead to accuracy you can rely on.
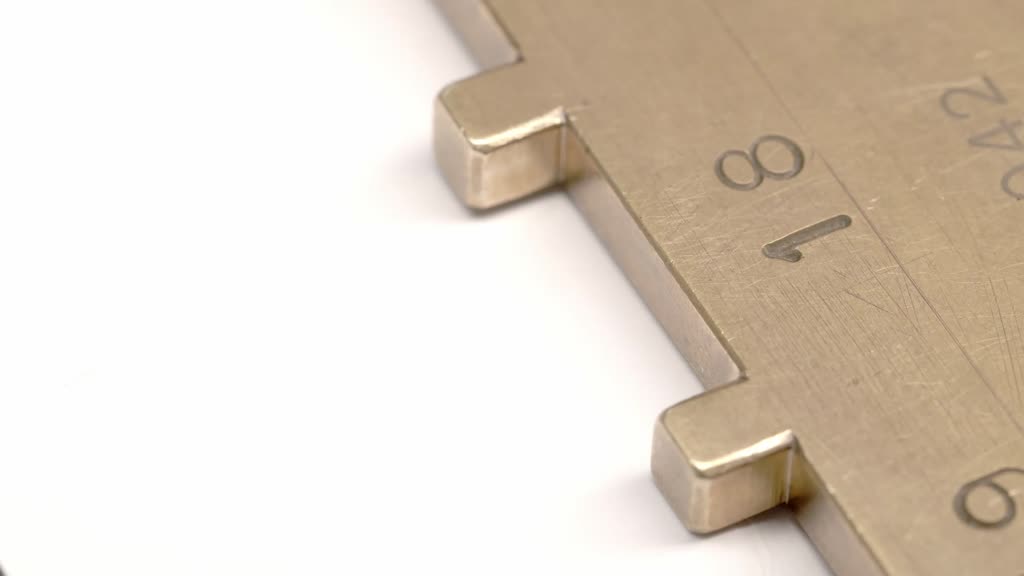
6.8. Gauging straps
The strap of a NOMOS watch must, above all, be comfortable to wear. The focus here is on how it feels to the touch. Smooth leather or suede? Horween Genuine Shell Cordovan or vegan Alcantara? Textile or metal? NOMOS now offers a whole range of different straps and bracelets in various materials, colors, and finishes. They must also undergo strict incoming goods inspections—no strap is exempt. In addition to meeting visual criteria, the correct lug width is also checked. After all, the strap should neither be too tight nor too loose on the lugs of the case. To ensure this, the straps are subjected to a gauge test. The end piece of the strap is inserted into the first gauge. If it fits, the strap is not too wide. A second gauge checks whether the strap is too narrow; it must not fit into this gauge. Simple, fast, reliable. Quality in no time at all!

6.7. Fixing the ellipse
The ellipse, the balance wheel's lever stone, receives the drive impulse from the anchor and keeps the balance wheel swinging back and forth. Today, however, it resembles a half cylinder more than an ellipse. Its radius and length are significantly less than half a millimeter—tiny, yet so important. The ellipse is pressed into the plate, which is a delicate step in the manufacturing process. Even the slightest breeze can carry the tiny rubies away. That is why we use negative pressure when positioning the components. This ensures that everything stays where it belongs. After all, the ellipse has to transmit six impulses per second, which is 518,400 impulses per day, and almost 190 million per year. It is amazing what this tiny component can do!
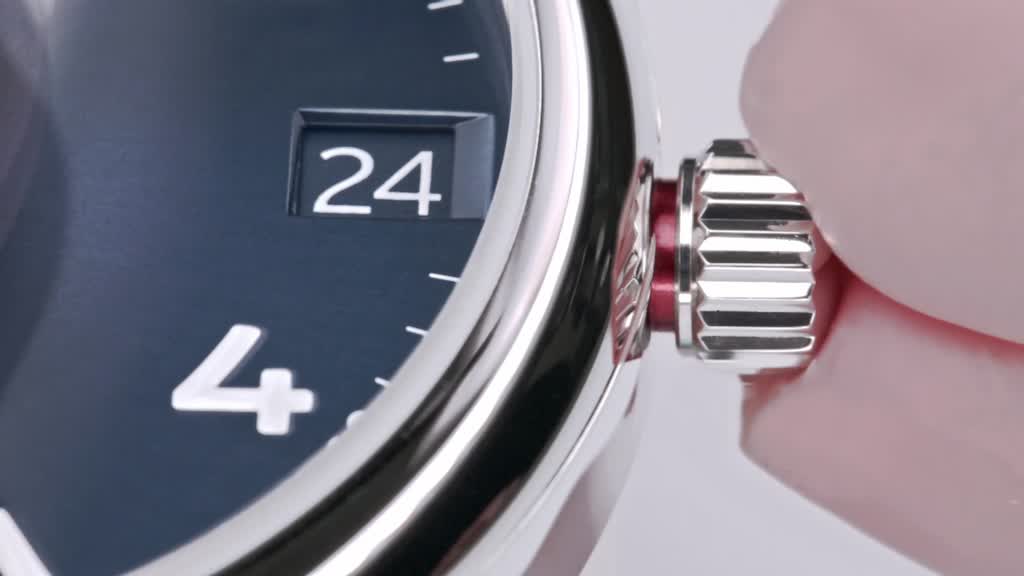
6.6. Testing the water resistance
NOMOS watches with a whale engraved on the case back are safe to wear while swimming. NOMOS tests the water resistance of its watches using various methods. In individual testing, for example, the watch is subjected to a specific air pressure—which should lead to a minimal deformation of the case. If no changes can be detected, pressure equalization has taken place inside of the watch, meaning that it is not water resistant. When testing several watches at the same time, the volume method is used. Each watch is placed in its own chamber, which can only hold a certain volume of air. This is precisely defined in advance for each watch model. If more air fits in, it must be flowing into the watch. Not good. But since quality at NOMOS has nothing to do with luck, this is extremely rare. If a watch proves to be stubbornly leaky, we send it to the diving station, as shown here in the film. The leak is then revealed underwater.
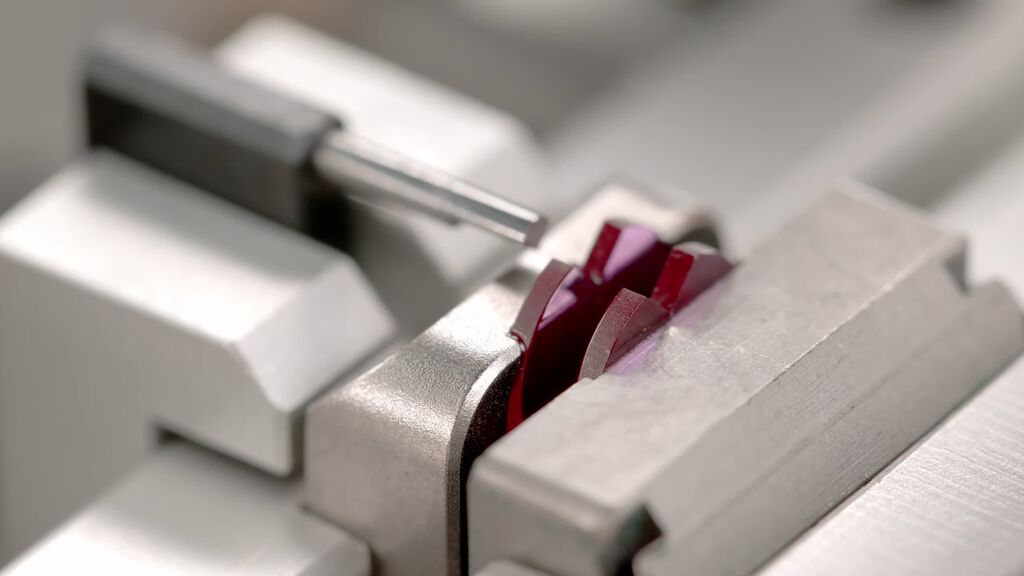
6.5. Evenness test
NOMOS movements are distinguished not only by their precision, but also by their exceptional thinness. This does not happen by chance. In addition to innovative designs and special material properties, the material properties of the parts, such as thinness and evenness, are also very important. In our movements, space for each component is limited. This means that the distance between neighboring parts is not very large. As a result, the wheels cannot move far up or down when turning—watchmakers say that they must turn with particular evenness. That is why, at NOMOS, each wheel is checked for evenness after the individual parts have been assembled: visually, using a camera system, and with extreme precision. This is the only way NOMOS can achieve perfect function in such a small space.
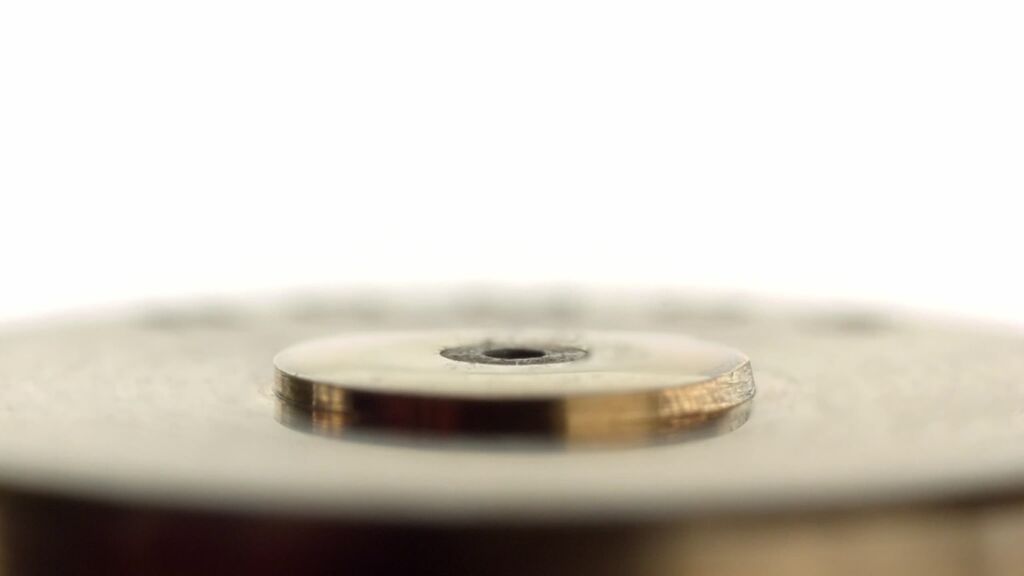
6.4. Pressing in the anchor shaft
The anchor shaft is a very short shaft with even shorter pins. Its dimensions and surface finish must be perfect. This is because the anchor plays a central role in the NOMOS swing system. It converts the rotational movement of the anchor wheel into a back-and-forth movement, which gives the balance wheel an impulse with every contact. This is actually just a small push. But it involves the transfer of force combined with acceleration, taking inertia into account. Friction also plays a major role. So everything has to be perfect! The anchor shaft, pressed in at just the right height, ensures that the anchor is perfectly positioned between the anchor wheel and the balance wheel. Rolled pivots reduce friction in the bearing, and particularly tight tolerances keep the anchor as straight as possible. So the anchor shaft, as tiny as it is, has a pivotal role to play in the overall accuracy of a mechanical watch.
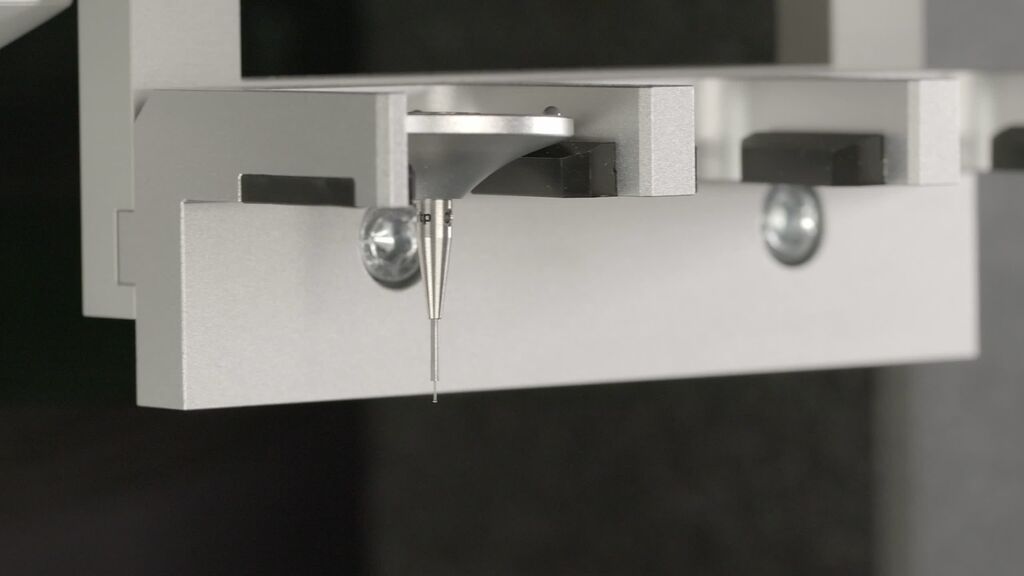
6.3. Quality assurance: tactile measurement
A tactile measuring method registers the contact of a body with a measuring tip. In other words, they get up close and personal. Modern optical measuring methods are very fast and very accurate. However, this is not always enough when it comes to manufacturing watch movements. Due to a wide range of influences—such as light, surface texture and reflections—the measuring accuracy of optical methods decreases in some cases. This is where tactile processes have the advantage. Whether inner or outer diameter, heights or entire contours, manual or fully automatic, almost anything is possible—if you know how. Only qualified technicians like those at NOMOS Glashütte know how to use the various measurement methods correctly.
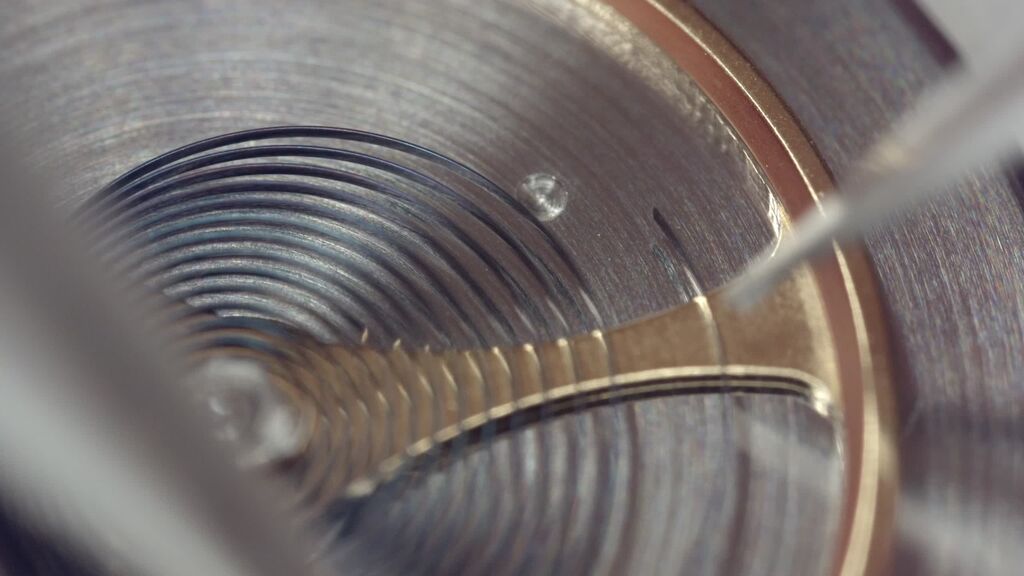
6.2. Adjusting the end of the balance spring
The last, curved part of the balance spring is known as the end curve. In the past, there was even an inner end curve. The end curve is used to attach it to the stud holder, and thus to the balance cock. In addition, the end curve is often used to quickly adjust the pace of the watch, because the frequency—which is the oscillation of the balance wheel—can be influenced by changing the effective length of the balance spring. To ensure that this happens reliably and in even steps, the end curve must have a perfect radius to the center point. This requires a keen eye, a steady hand, and a great deal of experience.
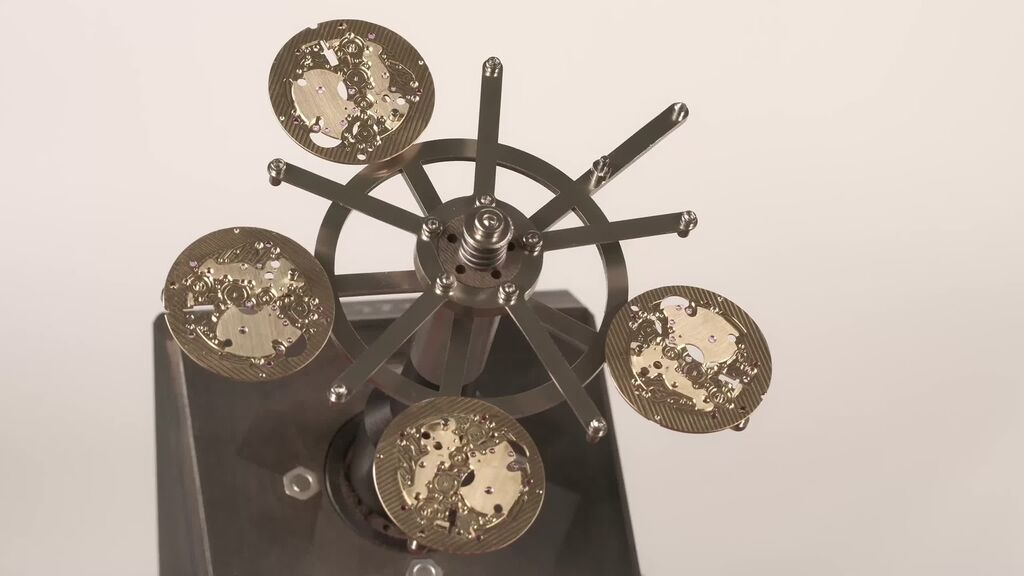
6.1. Sandblasting
Almost all of the framing movement parts at NOMOS are allowed to ride this carousel without having to queue: movement plates, three-quarter plates, balance cocks, and bridges. While they do, the parts also get a good sandblasting. But in a very gentle way—because it's not sand, but the finest bronze filings. This evens out the many different surface structures that result from the machining process. Not only does it look better, this also helps with optical measurement methods, creates an even surface for polishing, and smoothes some of the edges. And it's fascinating to watch!