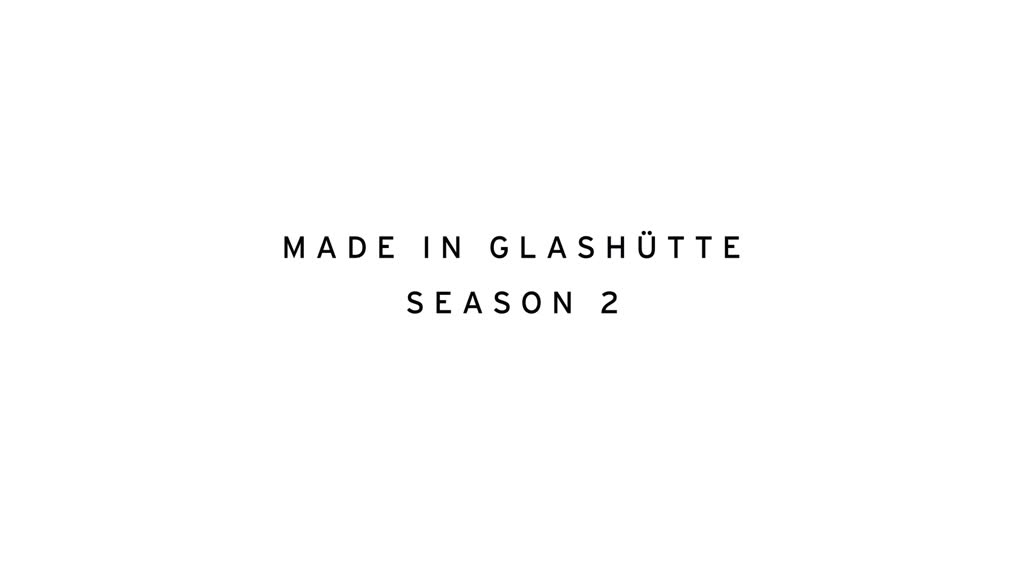
Made in Glashütte: Quality is audible
In the film footage from our workshop, you are also acoustically in the same space as our watchmakers and up close to every production step. You can hear the clinking of metal on metal, the blazing of heat, whirring of machinery, splashing of water, rustling of a starched smock, humming, drilling, pulsating, scraping, buzzing and grinding. All of these sounds go into the familiar tick-tock of a mechanical watch. And only once every production step strikes the right tone is the ticking in perfect harmony. Put your ear to your watch and listen to what otherwise cannot be heard. And stay tuned: the third season starts on April 2, 2023; follow us on the usual channels. You’ll find a compilation of the second season above.
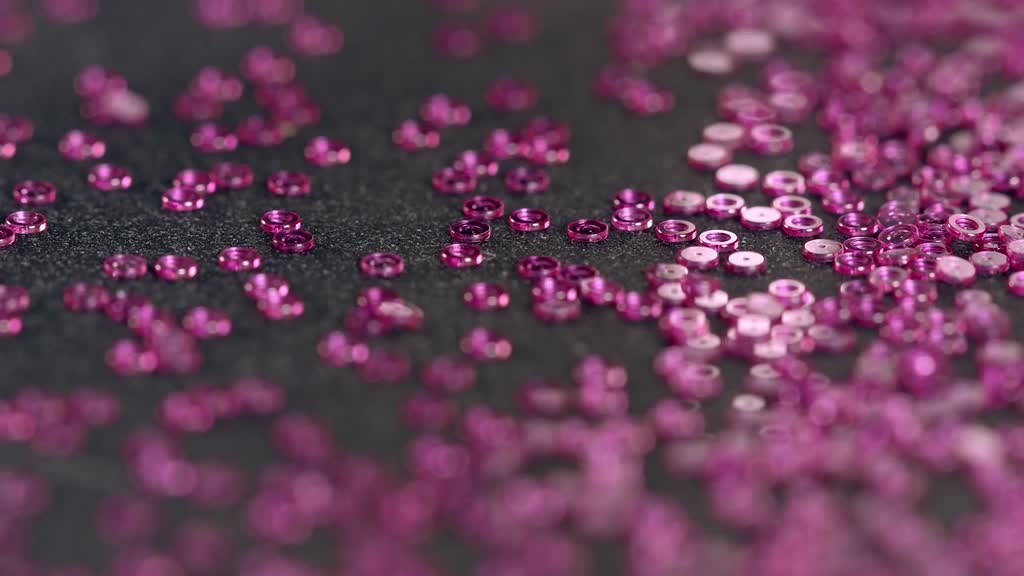
2.12. Filling the bearing stone magazine
Bearing stones made of synthetic ruby act as low-friction bearings for the wheels in our movement. However, to ensure that the wheels have sufficient play and do not jam, the small rubies must be pressed into the plates with an accuracy of just a few micrometers. By hand—only a job for the experienced, with very steady hands, a lot of patience and a good sense of touch, as the rubies are rarely larger than one millimeter and are up and away at the slightest draft. That’s why at NOMOS Glashütte, we use a machine to insert the tiny gems into the plates. In preparation, a little robot sorts the rubies into magazines, checking for the correct size and position so that no stone is pressed in the wrong way round.
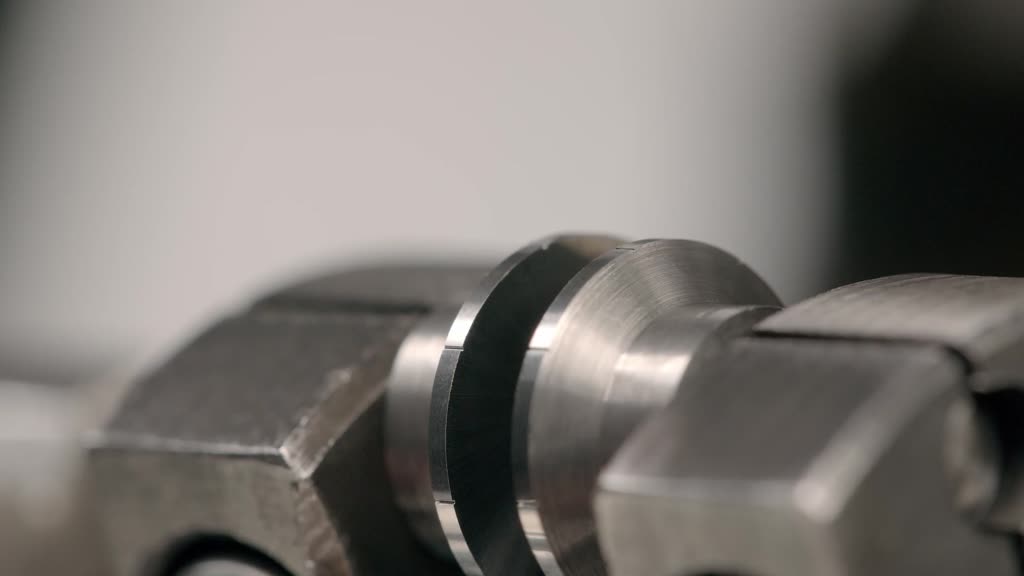
2.11. Burnishing pivots
Burnishing: one technology, multiple benefits. Precision and durability! Burnishing is pressure polishing for arbors and pivots that are subject to high stress. This technology can reduce the tolerance zone of the diameter of a pivot to 3µ—a very important requirement, especially for the balance staff and also for all other pivots that are set in ruby jewels. It also creates a homogeneous and, as a result of the pressure, very dense surface of the highest quality. This reduces friction to a minimum and achieves high corrosion resistance. Quality that lasts a lifetime.
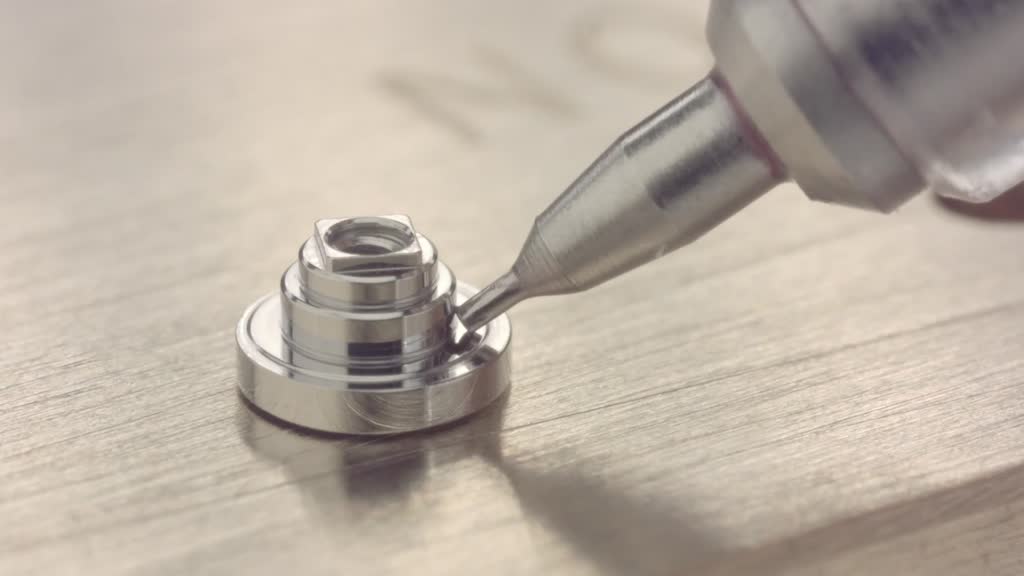
2.10. Inserting the barrel core
The barrel core bears the greatest load in the movement. Together with the barrel drum, it controls the tension spring, which stores all the energy. When the watch is wound, the tension spring wraps around the barrel core. As the watch winds down, this energy must be released very evenly. This requires the finest polishes and precisely the right amount of oil. At NOMOS Glashütte, we use small oil dispensers with a metering device. The even release of energy is extremely important for accuracy.
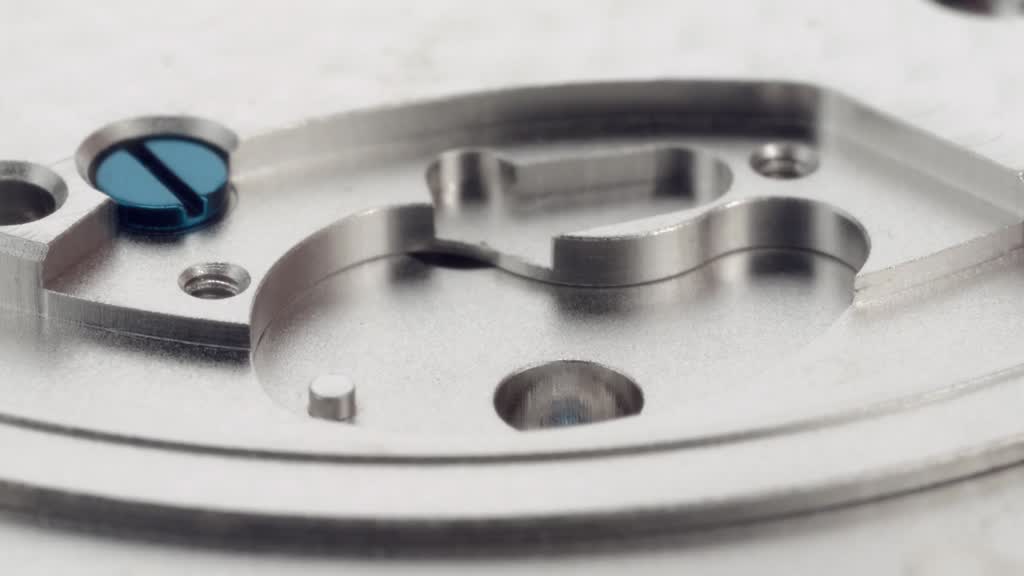
2.9. World time assembly - city disk
A journey through our planet’s time zones, and always with the correct time on one's wrist. Here’s how it works: The rest lever locks the selected location on the city disk, but this only moves in tandem with the hour hand, with each moving in unison. A place that is often several thousand miles away is just an hour for the hand. Suitable covers are mounted for the secure fitting of the city disk, ensuring reliable shifting and a sufficient distance from the dial. And so one always know what time it is at home; the hour disk shows whether loved ones are currently sleeping or having lunch, as the hour disk shows all 24 hours. After all, who wants to be woken up in the middle of the night!
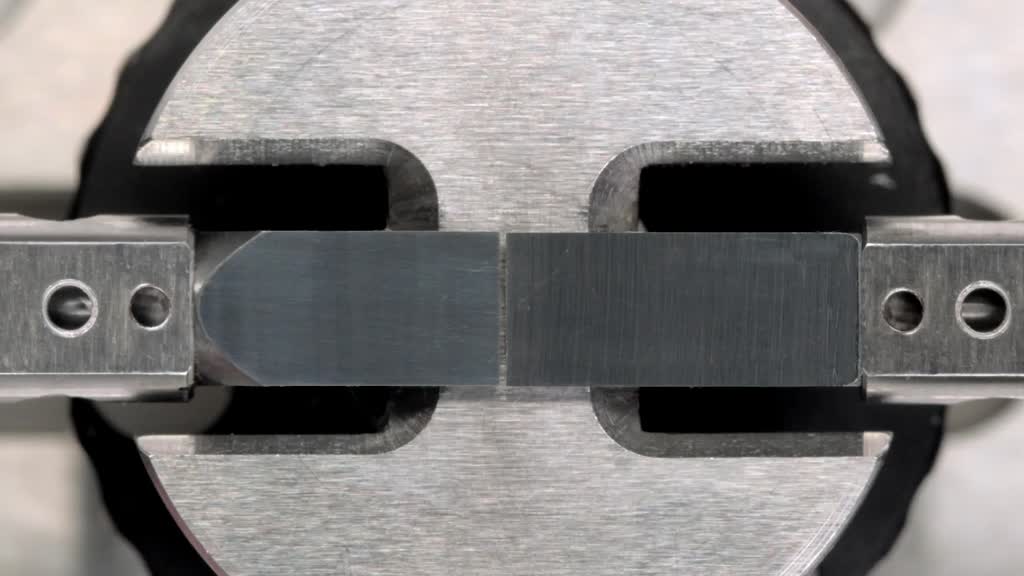
2.8. Measuring the outer diameter
The tactile measurement of an outer diameter. In this example, it’s the tube of the hour wheel. The diameter may only deviate by a few micrometers, otherwise the hour hand won’t fit. If the tube is too small, the hand can fall off easily; if it’s too big, a blued NOMOS steel hand could even pinch the tube so that it jams. The calculation of such tolerances involves mathematics and physics in the interest of quality. The implementation, the skill involved, is often an art form.
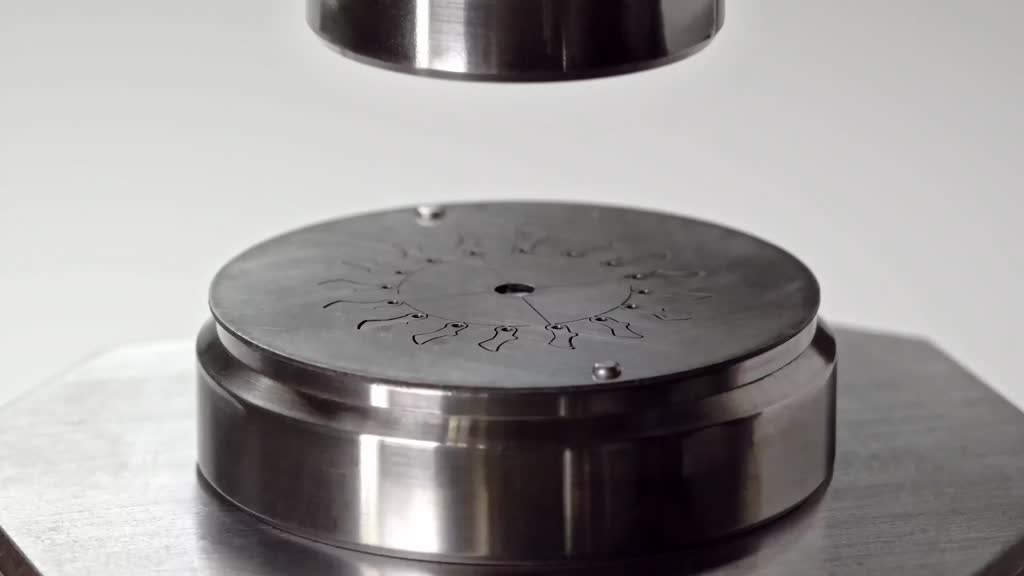
2.7. Electrical discharge machining parts from a blank
Tiny parts that are cut perfectly, using electrical discharge machining, remain attached to their holding burr so that they do not get lost in the machine. They then need to be separated, which means cutting through the holding burr. Cutting each part individually is also an option, of course, but this takes a long time. NOMOS always seeks the simplest and most efficient way. Using the punching process, all the burrs can be cut through at the same time. The date levers are then ready to be collected.
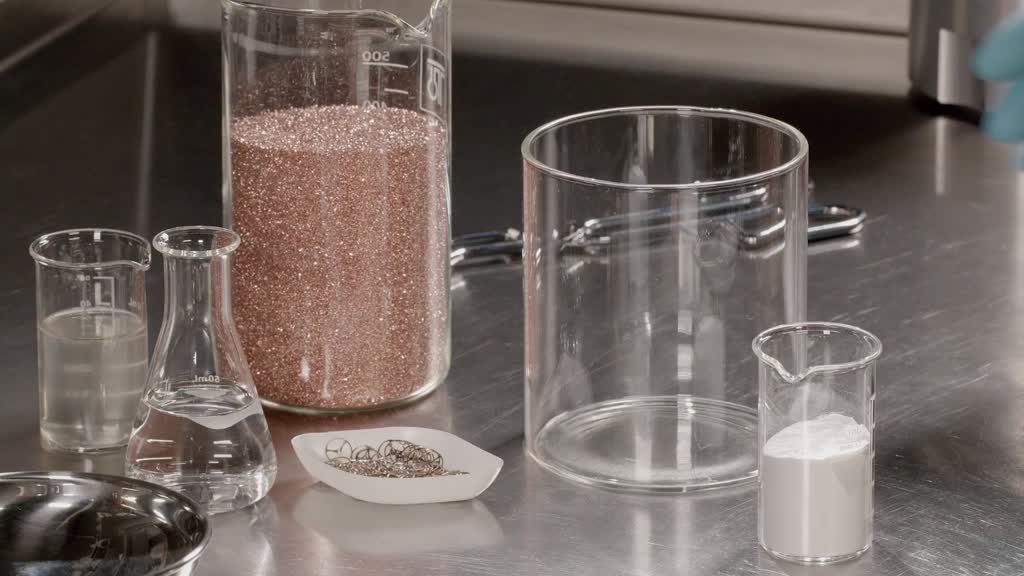
2.6. Polishing the balance wheel
Just like in a home kitchen, everything has its recipe. And exactly the right amount of each ingredient needs to be added, otherwise the soup becomes too salty or, as in our example, the polishing process is not stable. The right ratio of granules, polishing agent and the necessary liquid components guarantees polished and homogeneous surfaces when handled with care. Perfectly shiny, the next step is to gold-plate the balance wheel, providing the best conditions for later finding its matching balance spring, just like a pot finding its lid. Our work pieces are not only technically perfect, but also a feast for the eyes.
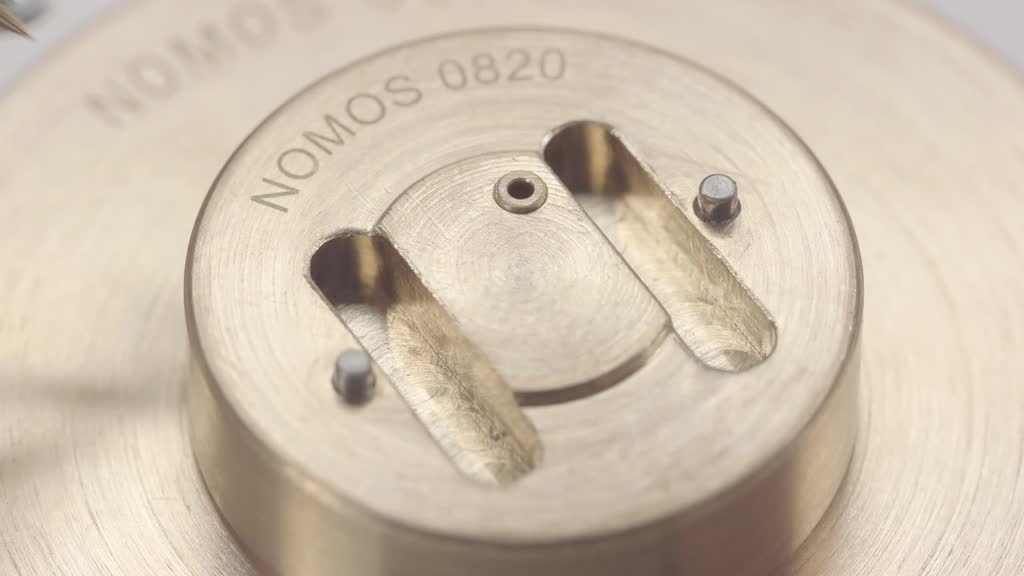
2.5. Assembling the regulator on the balance bridge
The regulator is used for the quick setting and adjustment of the watch’s rate. The first part of the NOMOS regulating system, which is mounted on the balance bridge, before being accompanied in the next step by our balance wheel with its beautiful, blue balance spring. A totally manual step, requiring the steadiest of hands.
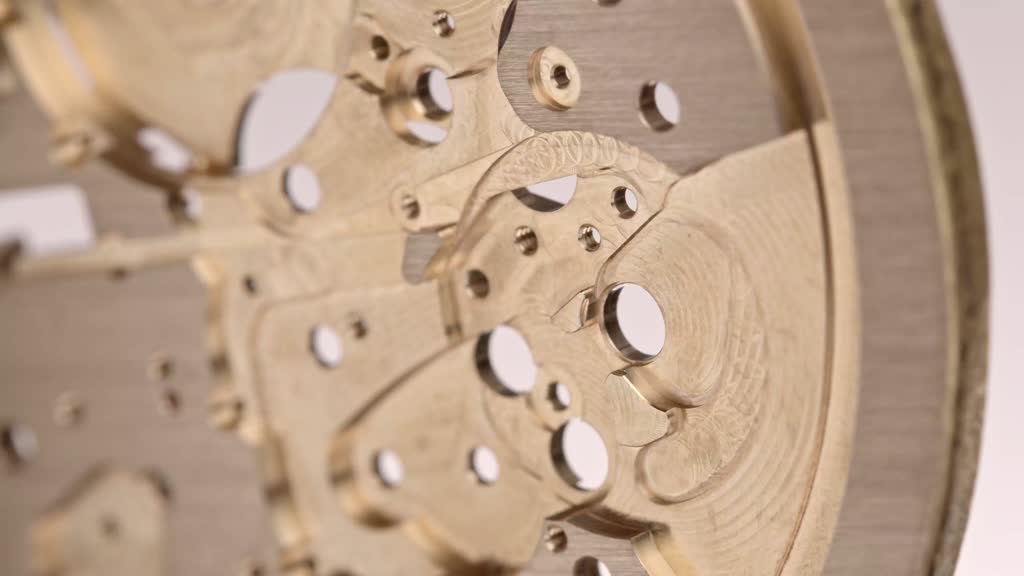
2.4. Drillhole testing
Gauging is a testing method that has a decisive advantage, especially for holes with particularly small tolerances. Optical measurement methods are subject to several influences such as edge detection, lighting conditions and reflections in incidental or transmitted light, and a number of other factors. With a plug gauge, either it fits or it doesn’t. And there’s often no more than 4µm in between. The drillholes must be perfect to ensure that pins, rubies and the shock protection have sufficient grip and that no burrs are formed. The best testing method is required in each case for this.
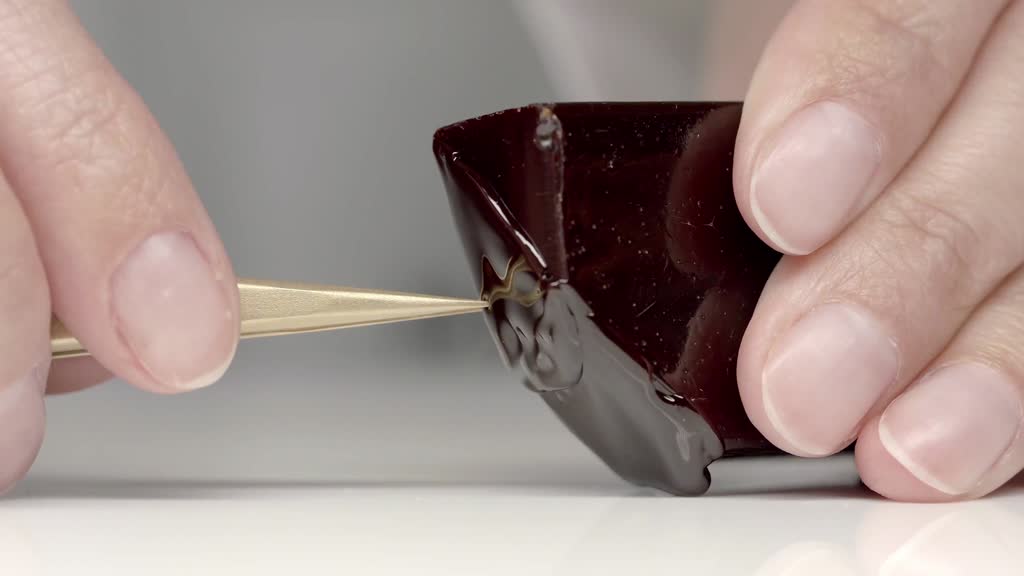
2.3. Pulling shellac threads
Even in today’s high-tech world, there are requirements that can only be met by the excrement of a louse. Hard to believe, but true! The female lac insect feeds on the sap of large trees, which she excretes as a resinous substance to protect the eggs she lays. After the young lice hatch, the resin deposit serves as the basis for the production of shellac. To secure the anchor pallets, we need a shellac quantity of approximately just 0.029mm³, or, in other words: the small portions we’re cutting here from our shellac thread have a diameter of approx. 0.21mm and a length of approx. 0.83mm. The louse measures approx. 1 to 2mm, so it is pretty big in comparison!
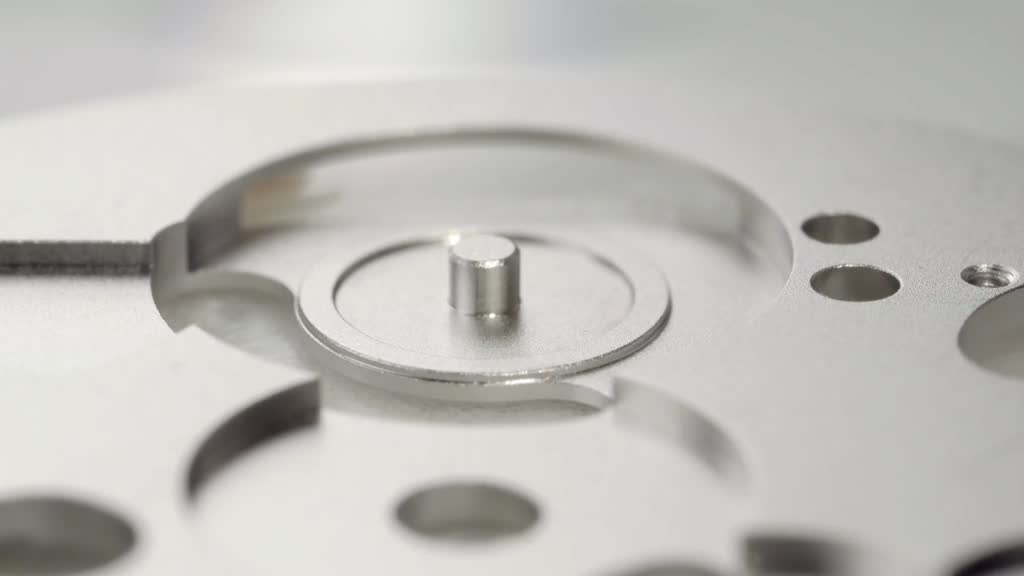
2.2. World time assembly – indexed wheel
Indexed wheel with corrector star and hour star. These two components make time travel around the world possible, and the hour star is needed to give the watch a local time. Using the button on the case, these two components can be used to correct the hour wheel in regular one-hour increments. The indexed wheel with corrector star also has to move the city disk. This takes one of 24 steps each time, while the hour wheel takes one of twelve steps. It’s a good job our mechanical engineers think of everything!
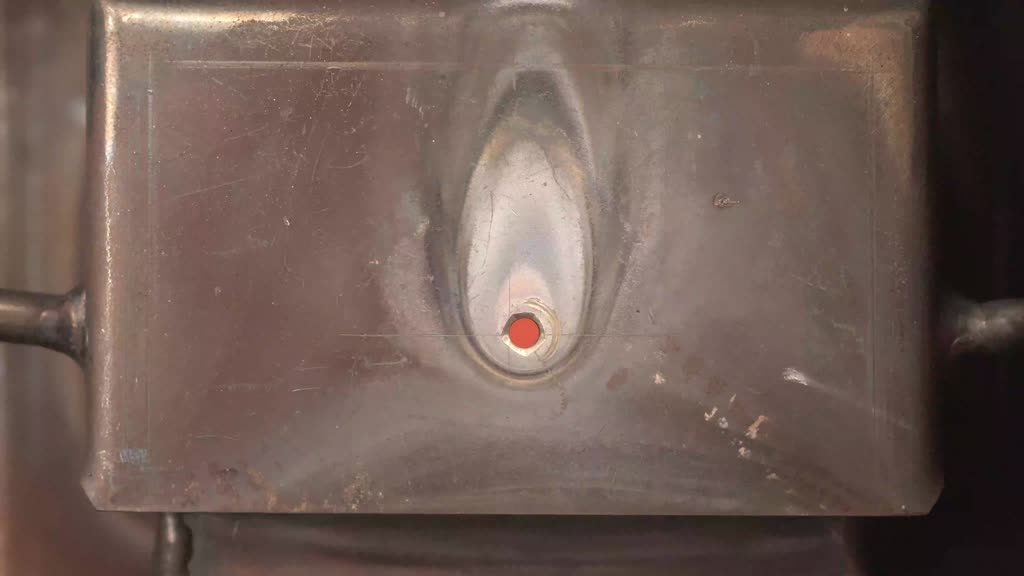
2.1. Hardening steel parts
Now things are really heating up! Since our camera would melt rather than shoot great films at 800°C (1472°F), we’ll show you this process in a more conventional way. Typical of many steel parts, the hardening of our crown wheel can be seen here. Annealing the steel parts and quenching them in cold water or oil alters the microstructure of the steel, drastically increasing the robustness of the material and achieving a toughness that is often referred to as “glass hard.” The material is now very brittle, and small parts in particular can break very easily. Therefore, hardening is always followed by tempering. Depending on the temperature and requirements, high wear resistance or also special spring properties are achieved. In watchmaking, “cornflower blue” has established itself as the typical tempering color, corresponding to a tempering temperature of 300°C (572°F). Our blue screws have undergone precisely this treatment.