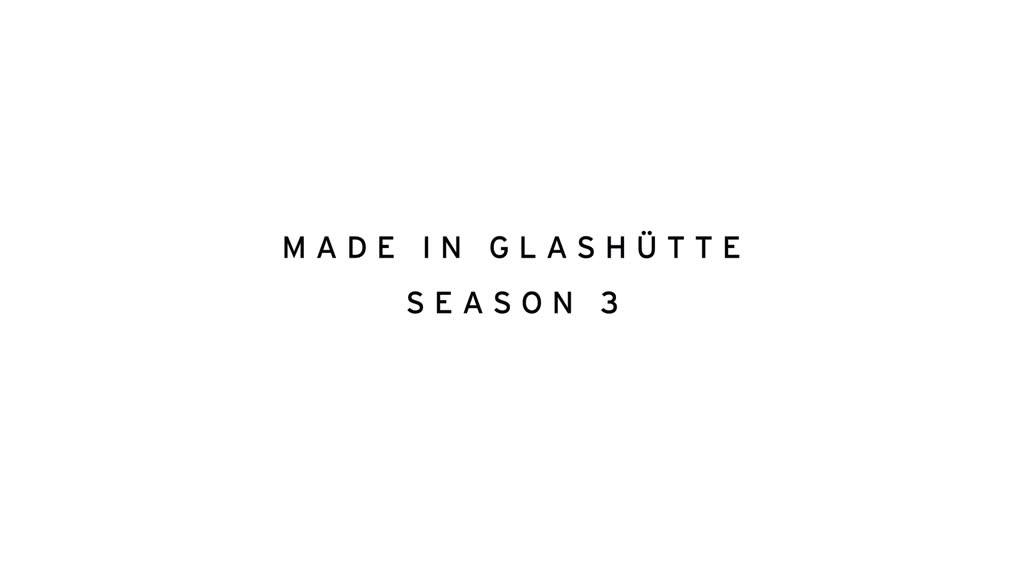
Made in Glashütte: Fine watchmaking by master craftspeople
NOMOS Glashütte, as these films make tangible, represents fine watchmaking by master craftspeople. An expert hand is the fine-nerved instrument at the other end of the tweezers, whose gleaming tip often appears in the picture. It is the tactile research unit that literally grasps connections. It controls processes not only with the correct method, but also with sensitivity and tact. Machines help to accelerate quality work, to secure and stabilize it. But it is the experienced hand that directs the orchestra of levers, discs, and drills—and lets the ensemble pause when results are more precise without machinery. Because not everything is about a micrometer, power, and repeatability. Sometimes, experience and feeling are what count. It is also the skilled hand, not the machine, that seeks new solutions. The hand may err once, but it learns in the process. This hand points the way to the future.
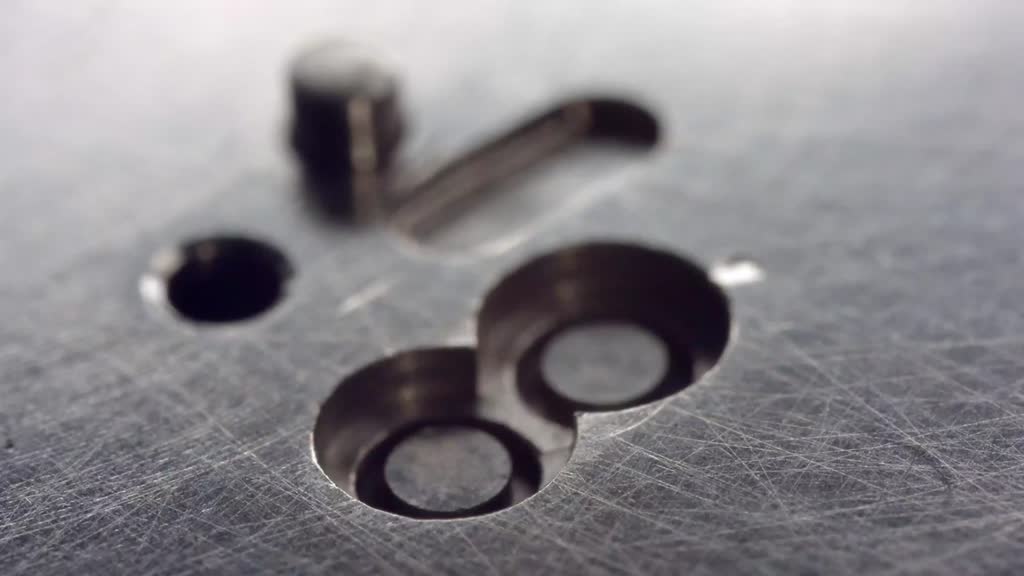
3.12. Sliding gear pre-assembly
The shape of the sliding gear in the automatic caliber DUW 6101 leaves a lot of room for your own imagination. We were briefly reminded of a wheelbarrow, as you can see in the film. And you? The tasks are, of course, quite different. The sliding gear ensures that, depending on the position of the crown, you can wind the movement, quickly adjust the date in both directions, and set the exact time. A tricky component for our designers, as well as for the production and assembly teams. The interaction must be perfect. It demonstrates outstanding teamwork, inside and outside the movement.
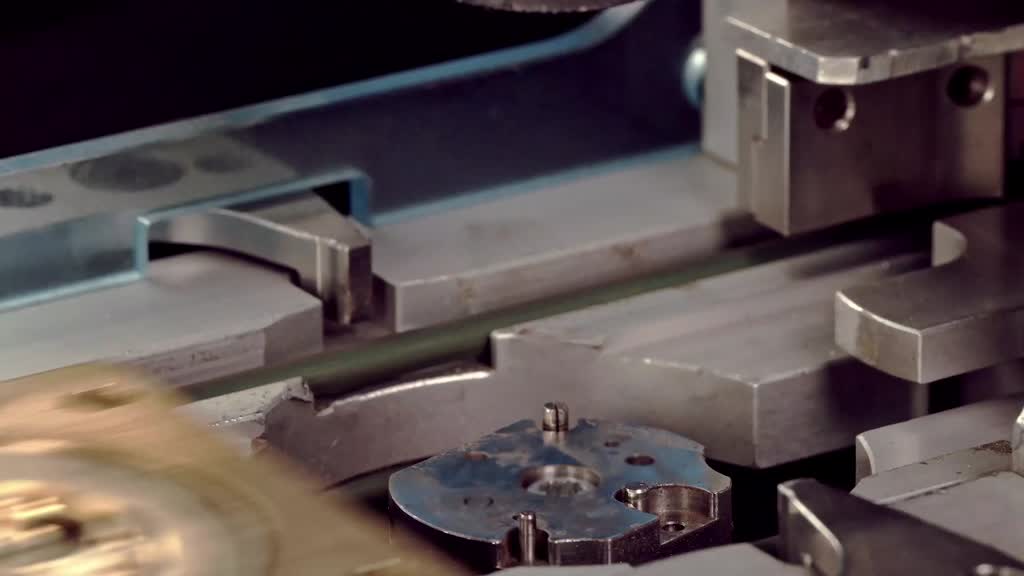
3.11. Turning out the base plate and milling the winding stem
The base plate determines the positions of almost all of the individual parts. Numerous borings, milled holes, planes, pockets, or chamfers are created in a complex machining process—from both sides. When almost everything is finished, the base plate can leave its blank. This process is called "turning out," which is when the diameter is cut to within a few micrometers, and the last burr is removed. Now comes another very important step: drilling for the winding stem. This requires a very long bore for precise guidance of the shaft. And since long drills like to find their own paths, NOMOS mills them in-house. This is how our production team ensures the quality of this special bore.
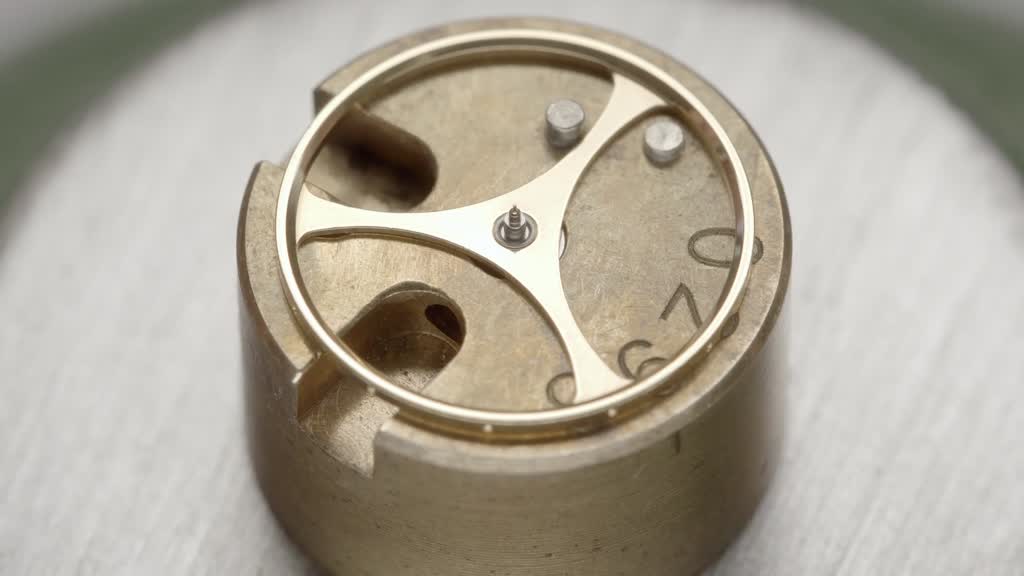
3.10. Fitting the balance spring
The tempered blue NOMOS balance spring with its collet in the center is placed on the pre-assembled balance cock and gently pressed in place with a tool. Not just any old way, of course, but at a very specific height and at a very specific angle to each other. The balance spring and balance cock were chosen for each other beforehand. Sorted according to specific characteristics, perfectly matching pairs are formed. In the past, balance cocks were fitted with balance springs that were clearly too long. The balance spring was then gradually trimmed until the desired frequency was achieved. Perfect for each individual watch, but rather laborious. With today’s production technologies, we can manufacture to such tight tolerances that, after sorting, each balance bridge finds its matching balance spring.
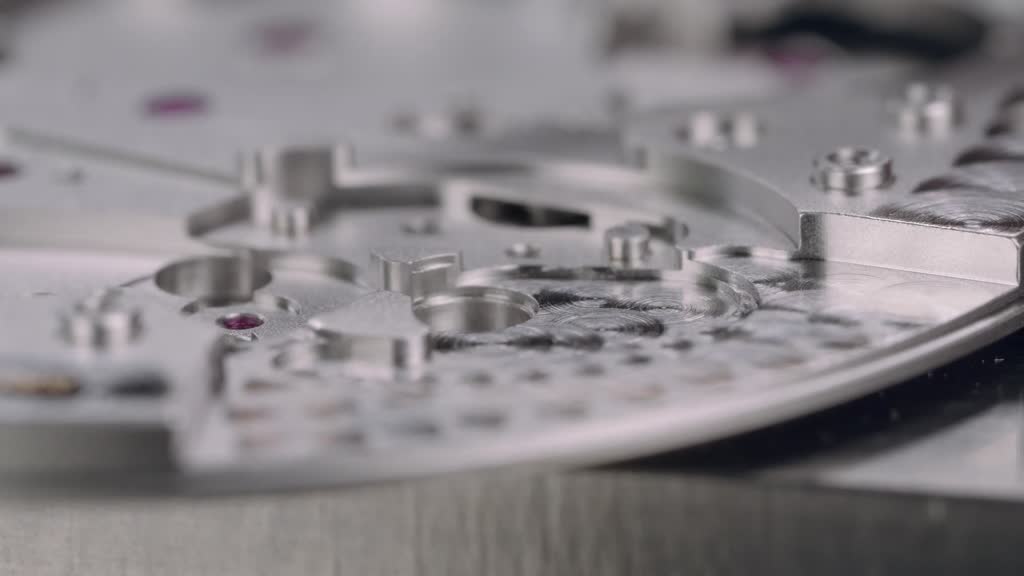
3.9. Pre-assembly of the base plate
Numerous tiny parts are pressed into the base plate, the basis of every movement. And this is done with an accuracy of just a few micrometers. The exact position of the rubies, for example, ensures that the wheels are sufficiently spaced apart. Our designers calculate everything extremely precisely so that the movements are as thin as possible. After all, this is what makes the elegance of our watches possible. For the assembly process, our technological specialists have come up with special devices that ensure the press-in dimensions of the individual small parts. This allows for quick assembly while maintaining the best quality.
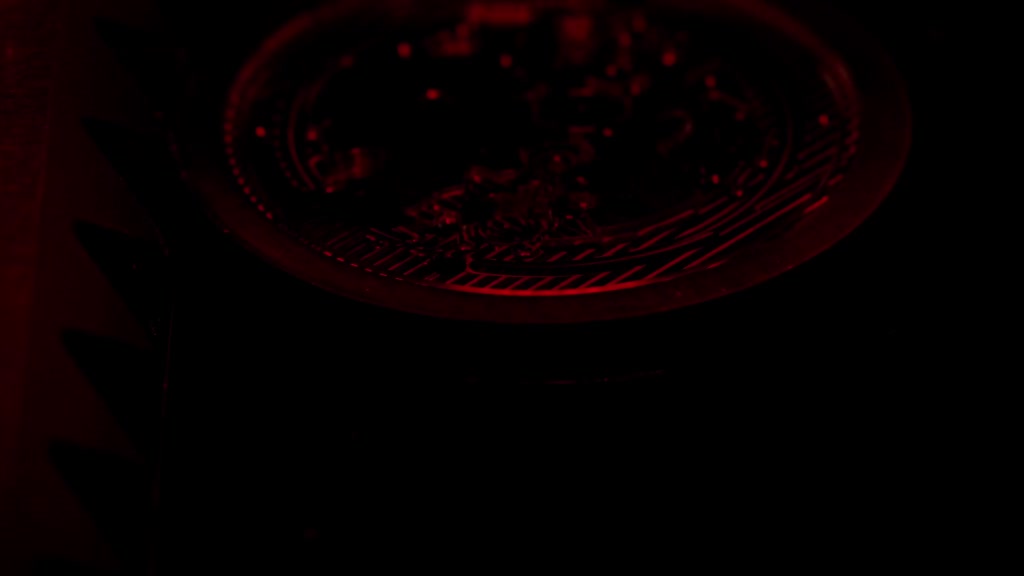
3.8. Video measuring machine
Optical measurement with a video measuring machine enables us to check decisive locations and diameters very quickly and reliably. Due to its programmability and speed, a very large number of parts can be measured automatically during production, which is essential to ensure a high quality. However, non-contact measurement is not suitable for all requirements. Traditional measurement by hand still retains its necessity, as some milling patterns or surface reflections can influence optical measurements. Which specific measurement methods are used is decided by our measurement engineers, based on their many years of experience.
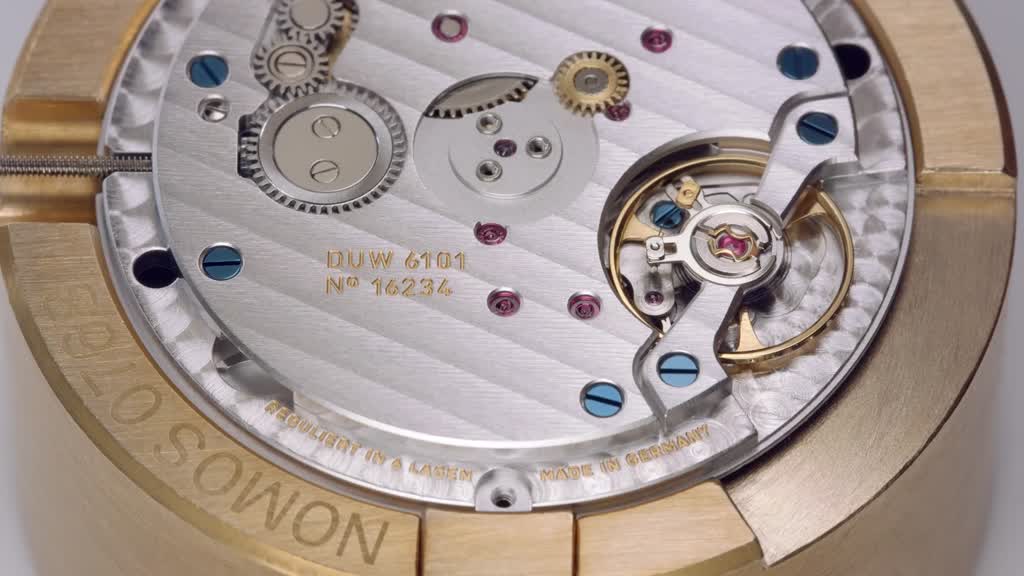
3.7. Assembling the rotor
Flat and elegant, the rotor nestles against the DUW 6101 movement. And yet it provides sufficient mass and size for its function, thanks to our design engineers. The rotor ensures the automatic winding of the watch as soon as the latter starts moving. The larger and heavier it is, the easier it is to supply the movement with the energy required. Through a sophisticated design, our engineers have managed to increase the efficiency of the rotor significantly. Energy efficiency—a current topic in a very traditional form.
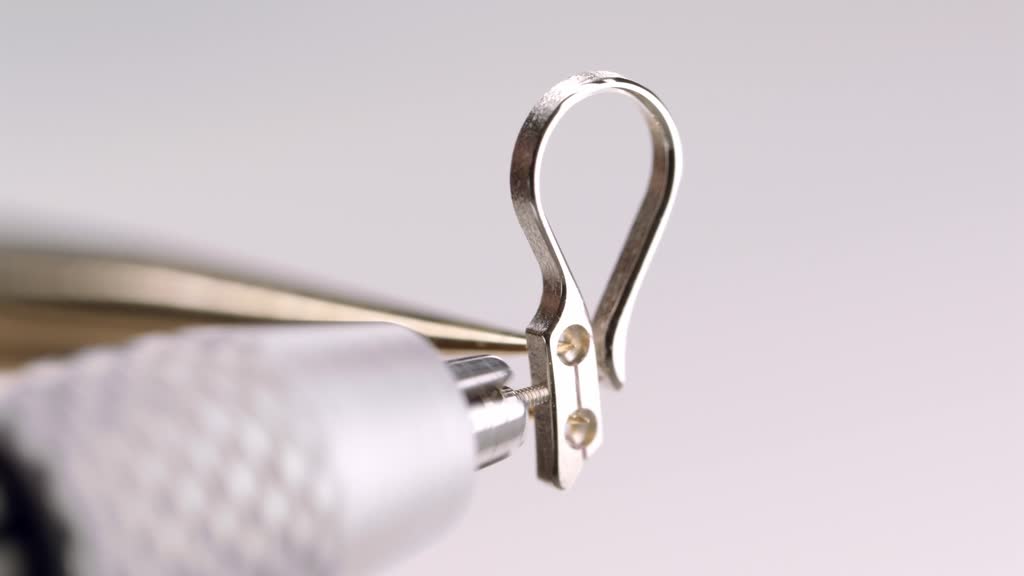
3.6. Assembling the swan neck fine adjustment
A feast for the eyes! A regulating spring in its most beautiful form, a swan neck, represents Glashütte tradition at its very finest. Polished edges, the rough outer surface, and black polishing of the surfaces require a great deal of skill, experience, and patience. Along with the regulator, this part allows the pace of the watch to be adjusted very precisely. If this was not enough already, this interaction takes place on the hand-engraved balance cock. Lovingly produced in Glashütte.
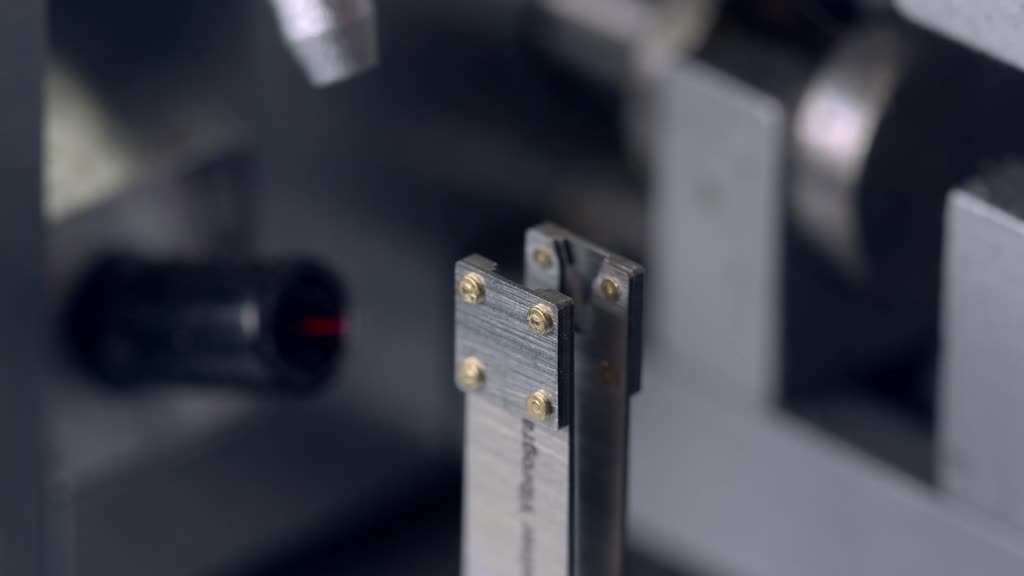
3.5. Statically balancing the balance
Everything must run smoothly! You probably know from cars that when a wheel has an imbalance, the steering wheel starts to wobble. Thus small weights are attached to the wheel to eliminate the imbalance. With a watch it is quite similar—only much, much smaller. In the past, an imbalance was determined with a balance scale. The place with the biggest imbalance always points downwards. Then you had to remember the spot and then remove material from the balance wheel using a drill or countersink. This was done until the balance wheel always stopped at different points after turning on the balance scale. Patience was needed here. Today, we use a helpful technique again. Here, the balance is driven evenly by an air current. A sensor and a laser localize the position and size of the imbalance, the device remembers the spot and mills off little or a lot of material accordingly. Yes, the device is much larger today than it was back then—about 3,000 times larger, in terms of volume. But it is also much, much faster.
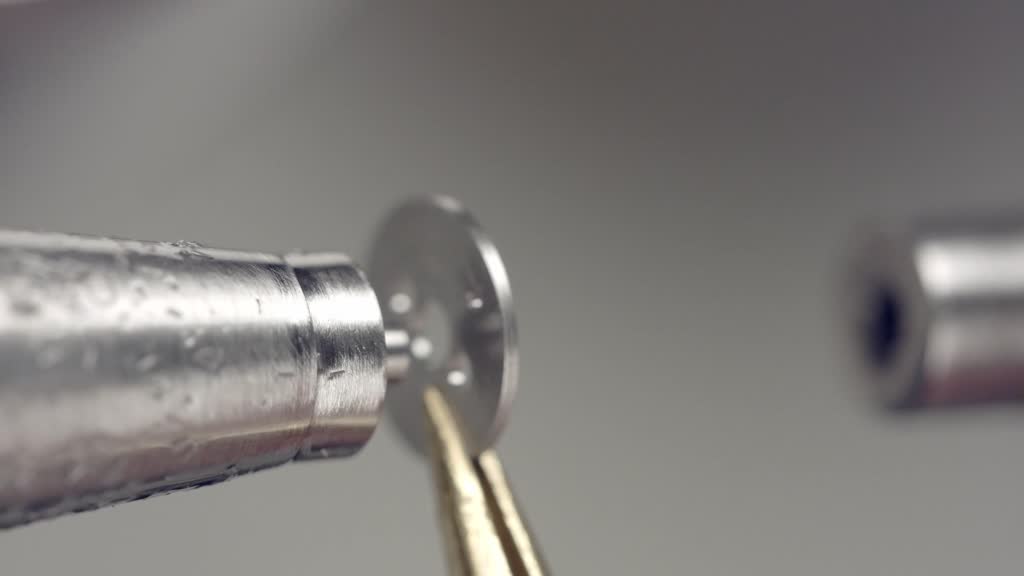
3.4. Hobbing the corrector wheel
As part of our world time watch, the corrector wheel allows the hour hand to be adjusted incrementally when traveling. This requires a very special tooth shape as the corrector wheel turns constantly with the hour hand. And the wheel needs to be ready to jump to another time zone at any given moment—no easy feat! After all, time travel is rather special.
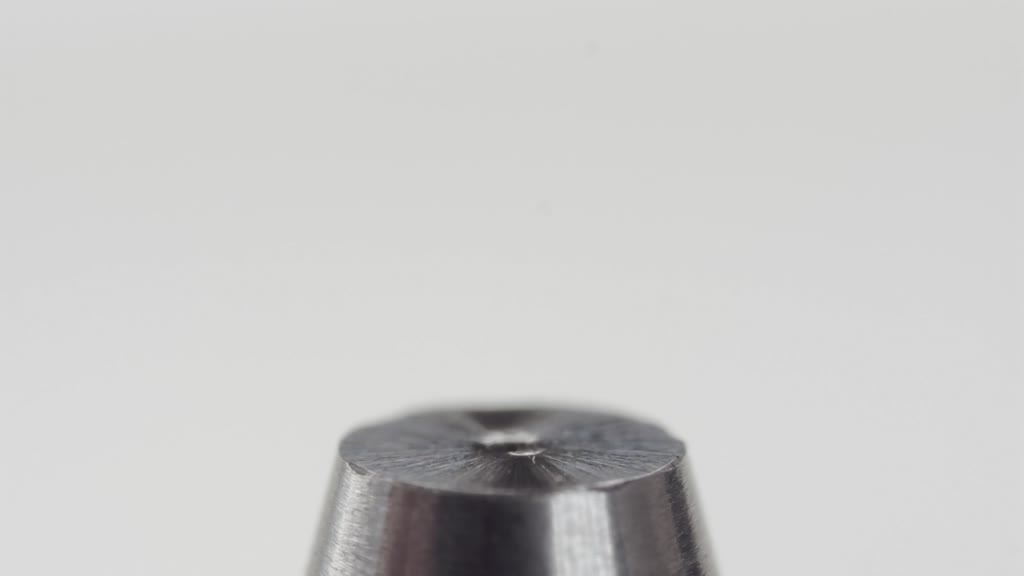
3.3. Riveting the escape wheel
As a part of the NOMOS swing system, the escape wheel is at the heart of the movement. The pallet only releases the escape wheel to move step by step—a constant stop and go, or the famous tick-tock of a mechanical watch. The energy of the tension spring is delivered to the pinion via the movement; the wheel is released and stopped again 21,600 times an hour. The rivet connection between the wheel and the pinion needs to last a lifetime. This labor of love is only possible with knowledge, experience, skill and a passion for detail.
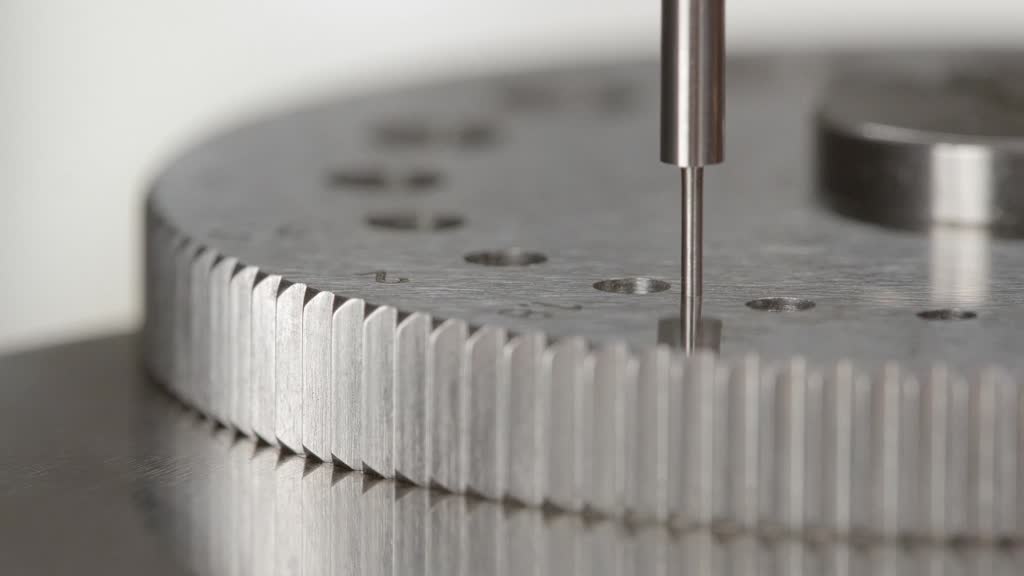
3.2. Height measurement
The hour wheel sits directly beneath the dial and has the honorable task of supporting the hour hand. As our movements are especially flat, the height of each individual wheel must be thoroughly checked. Only then can we achieve the combination of slender elegance and reliable function. Every single part makes its contribution.
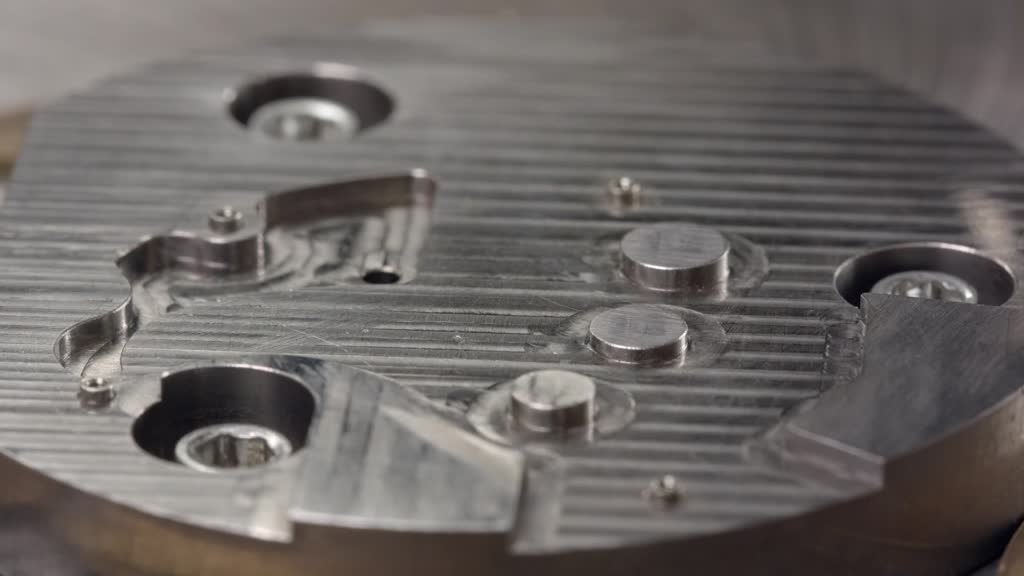
3.1. Sunbeam ribbing
A very special finish for our most beautiful calibers. While the stripes on most movements are arranged in parallel, the beams here all radiate from the same point. This results in an effect that is akin to the rays of the sun. And what could possibly be nicer than always wearing a glint of sunshine on your wrist!