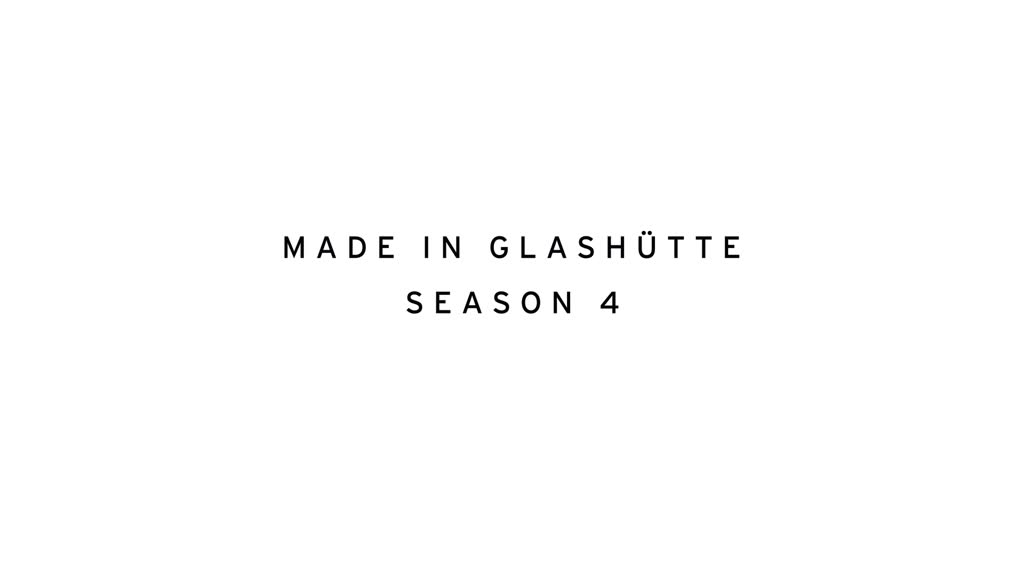
Right up close
In the close-up of the film sequences, you not only see something happening in our facilities, but you experience it happening. The close-up view illustrates the need for expert care in every single step of the process. In the intimacy of magnification, surfaces become recognizable as landscapes with a topography that is immediately altered by each intervention. You see how a plate begins to vibrate very gently under pressure. How a gulf can open up under an engraving pen without further ado. But there is also pure joy in how the tiny cogs in the world of the movement circle as radiant suns. And a most beautiful reliability in the inevitable flow of an oil droplet spread on the corrector wheel during pre-assembly. The microscopic perspective is surprising and essential; it is artful, authentic, and very satisfying.
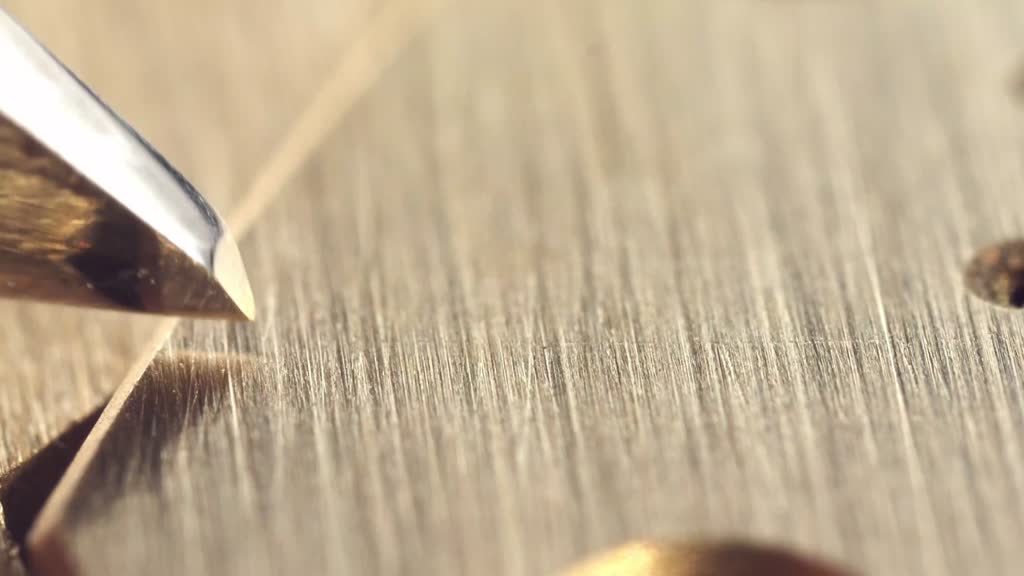
4.12. Hand engraving the balance cock
As if hand engraving weren't enough of a challenge, at NOMOS Glashütte it also has to have a personalized touch. We've set the bar very high for ourselves here, because mistakes cannot be corrected. What's engraved stays engraved, and Tipp-Ex can't help. Only a perfect result is good enough for us. This requires experienced specialists with a sharp eye and a particularly steady hand, as well as the perfect degree of force. In addition, an engraving tool with extremely precise geometry, sharp cutting edges, and perfect surfaces. But all this only leads to perfect engraving if the engravers at NOMOS can feel the material. This is the only way to create the details that makes our balance cock shine. Made with a lot of love.
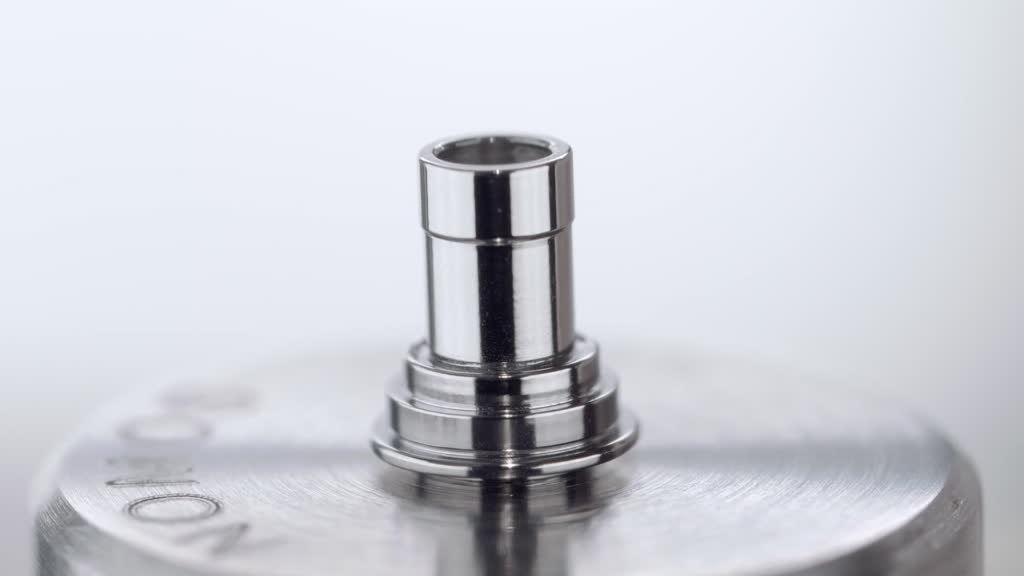
4.11. Pre-assembly of corrector wheel
Only the corrector wheel makes world travel possible. In our world time and GMT models, the corrector wheel enables the hour hand to jump by exactly one hour: from one time zone to the next. Nevertheless, the hour hand continues to move continuously. The hour jump is added to the continuous rotation. The corrector wheel consists of five different components that are joined together. The shaft of the hour hand is riveted and holds the whole package together. Since the parts have to move slightly for the hour jump, a lot of care is used here to assemble, oil, and rivet. Now it's time to start time traveling around the world. Let's do the Time Warp again!
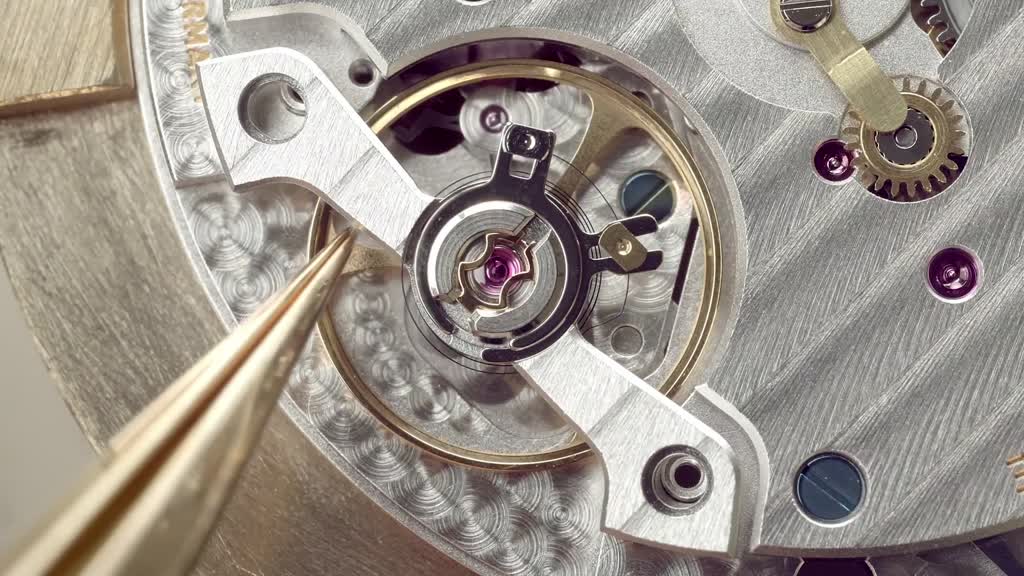
4.10. Inserting the reglage
The small act of creation: the movement begins to tick. The reglage, consisting of the balance bridge and balance, is inserted into the movement. Now it becomes clear whether all the preliminary work has been carried out to the highest standard. The accuracy of a watch depends on many factors. Is there sufficient force applied and does each wheel have enough play? Can the lever transmit the power from the gear train to the balance wheel with as little loss as possible and cause it to oscillate? That's half the battle, because what oscillates can also be regulated! How do the oscillations behave in the individual positions? Is the play in each case perhaps too large? Or are the vibrations too wide and the movement begins to gain time? Countless questions that our reglage experts ask themselves if things don't work right away. Experience is the best advisor here. Highly qualified and motivated employees ensure perfection and precision. Knowledge, experience, and skill—resulting in handmade quality!
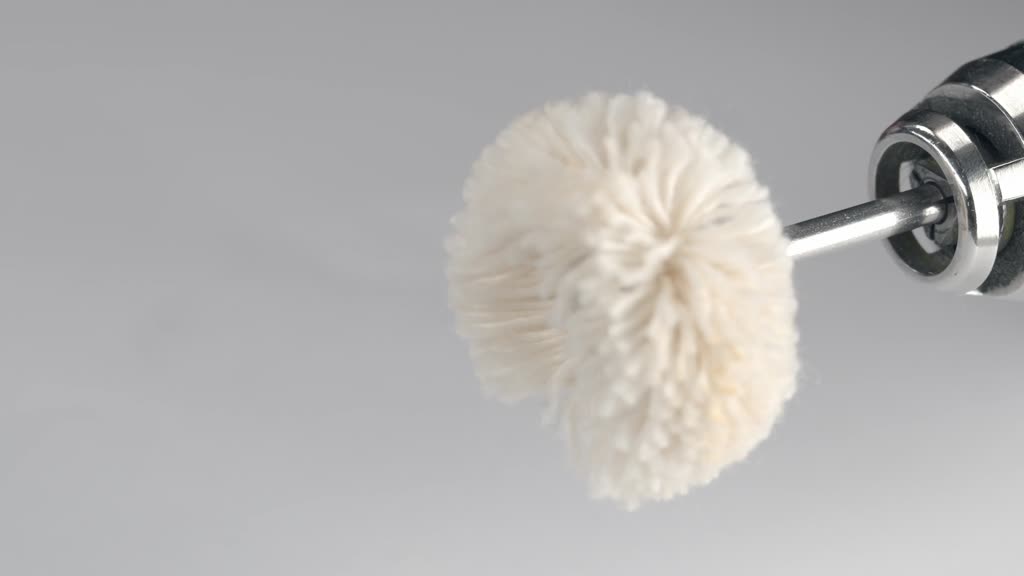
4.9. Polishing the case back
A handy mirror on the wrist: The polish of our cases invites you to take a look at your reflection. So even watch models with stainless steel backs have something to discover on the inner side—yourself. Models with rounded cases are particularly interesting, as the mirrored surface often reflects a distorted image, due to its curvature. But this is only possible if the polish is absolutely free of scratches and streaks. That's why our specialists in Glashütte take special care when it comes to the final polish. There are many ways to have fun with NOMOS watches!
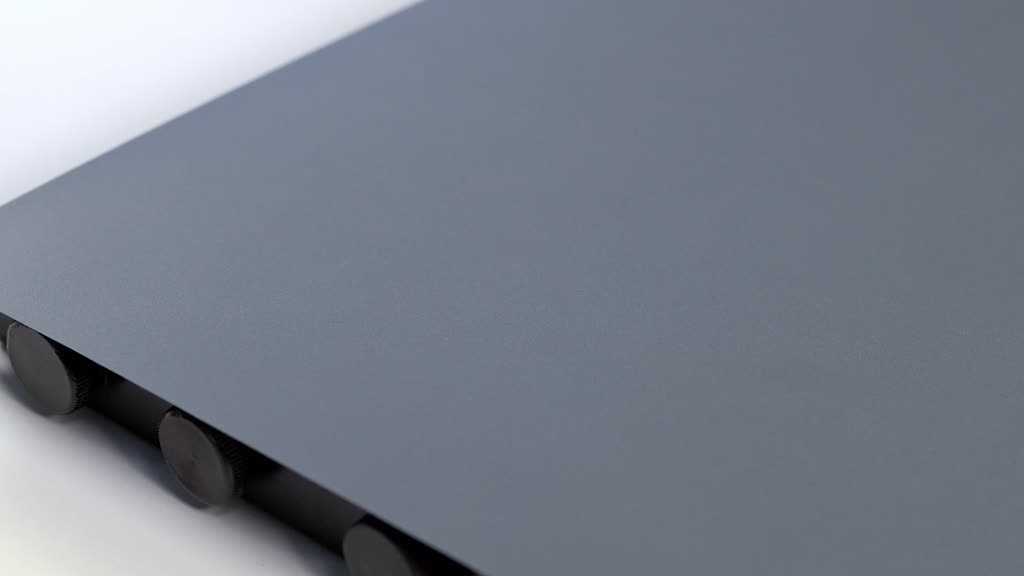
4.8. Honing the blank
Looks simple, and it is—but extremely important! Three-quarter blanks or, as in this example, work plates are milled from blanks. The light honing on both sides is used to remove the last metal shavings after drilling, milling, countersinking ... If even one chip of metal remains, it can have severe consequences. During quality assurance, parts are repeatedly inspected with a magnifying glass and measuring machine. Metal chips can affect the measurements, which in the worst case can lead to a flawed machine correction. The result would be reject parts. It's good to know that our production specialists are aware of all these things. Quality from the first step!
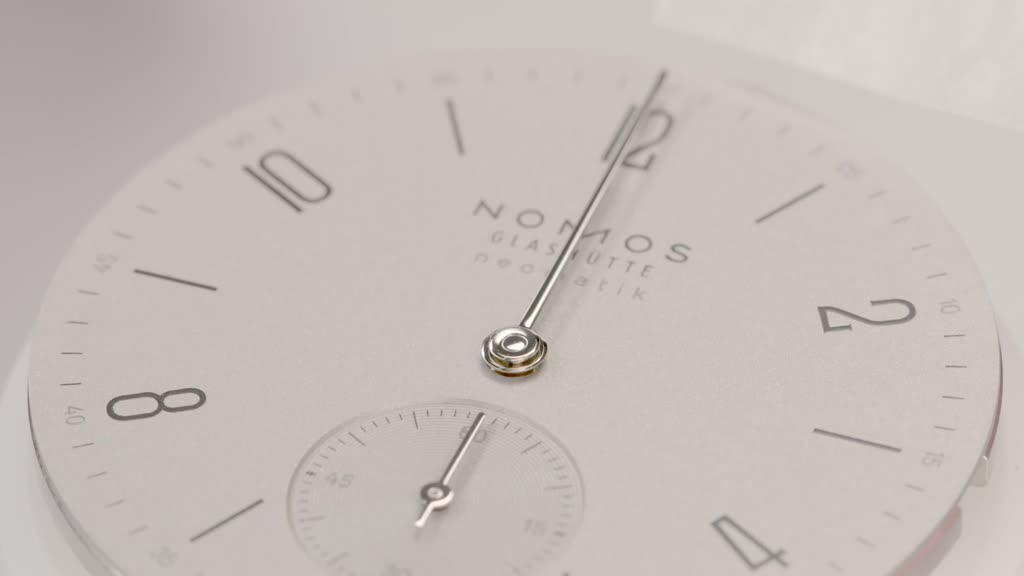
4.7. Removing the hands
Not only the assembly of a watch, but also its disassembly must be learned. After all, if you take your watch in for regular inspection, you'll enjoy it for a very long time. Before the movement can be inspected, it must be removed from the case—and the dial and hands must be disassembled. Removing the hands, in particular, requires a great deal of dexterity. With experience, a steady hand, special tools, and some tissue paper, the hands are lifted off the shafts. It is very important that this happens without any marks or damage. At this point, it becomes clear that NOMOS also places a special emphasis on quality when servicing each watch.
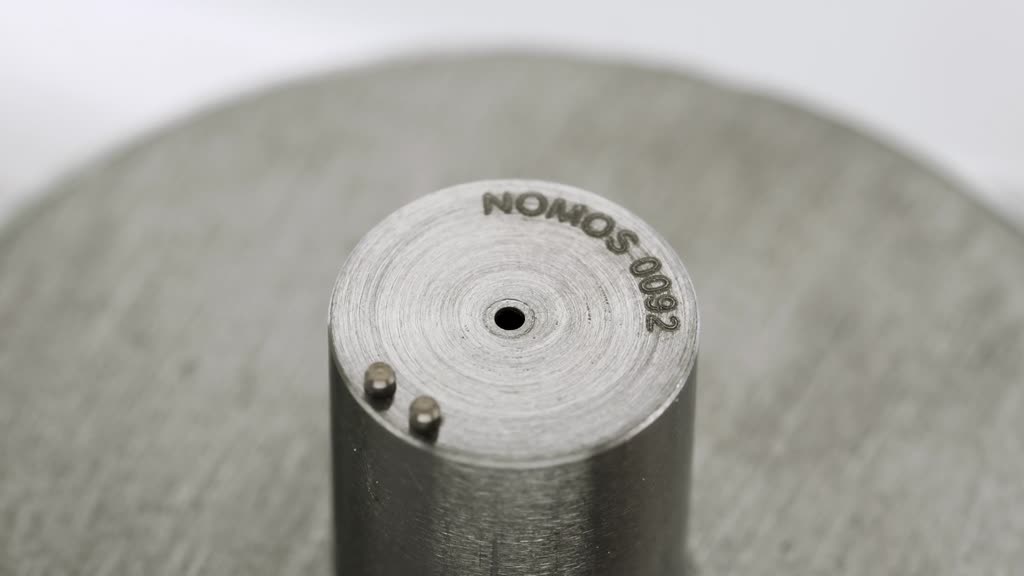
4.6. Pressing on the plateau
The plateau is also called the double roller. It contains the ellipse, that small ruby from which the balance gets its force impulse. And it does so every half oscillation. In addition, the plateau serves as a safety device, so that the anchor always remains on the "right side". The manufacture and assembly of the individual components must be very precise; after all, this is the heart of the movement. Only a perfectly composed interaction enables the watch to run precisely.

4.5. Assembly of the power reserve and dial
A charge display for mechanical watches? You can find it at NOMOS Glashütte. We just call it something else: the power reserve indicator. In a purely mechanical way, it provides information on the dial about the remaining energy stored in hand-wound watches. This elegant, patented complication only requires three additional movement parts. When the watch is being wound, the crescent-shaped indicator responds by withdrawing the red area from sight. When the red area has disappeared completely, the NOMOS watch has energy for at least 42 hours. That is its power reserve. To prevent the power reserve discs from brushing against the dial, their vertical play is limited by a large gold-colored spreading spring. When the power reserve indicator is filled with red, the watch must be wound again with the crown; analogous to charging the battery, except that it happens a lot faster in our watches.
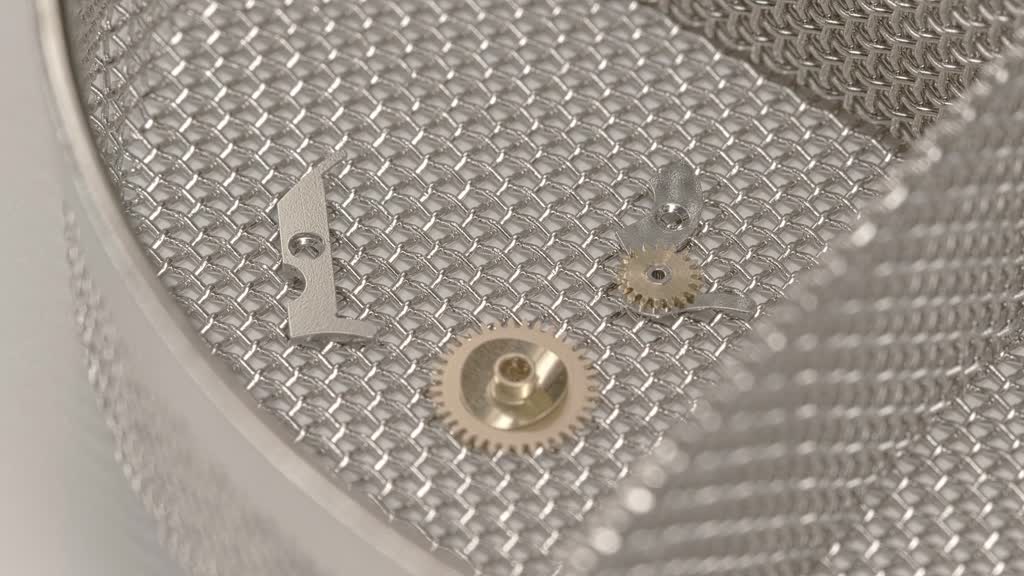
4.4. Washing
Laundry goes in the washing machine. And small watchmaking parts? There are washing machines for them as well, even if the machine looks a bit different. The small parts are placed in it and the program can start. From the washing solution with optional ultrasonic activation, the journey continues through several rinsing solutions that remove the very last droplet of water and last grain of dust. The washing basket is constantly rotating, just like a washing machine at home. The final stage is, of course, the spin cycle. And then there's the dryer with warm air, which dries the items immediately—very practical! Hanging them up to dry is not an option, as clothespins are simply too big.
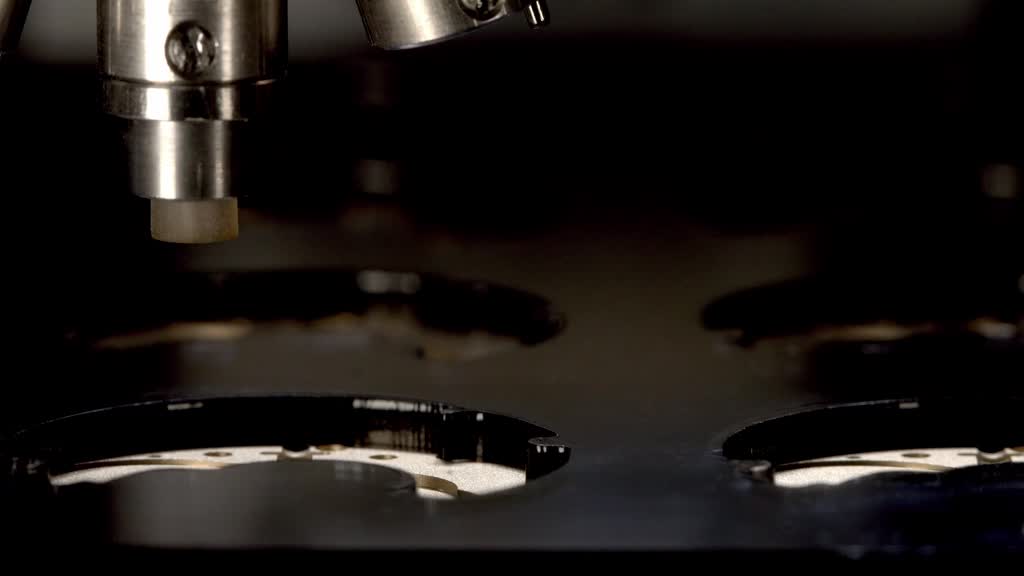
4.3. Setting bearing jewels
Small rubies enable low-friction bearing of the wheels, or more precisely, the pivots. Being pressed in at the correct height guarantees that each wheel has the necessary clearance to rotate freely. Hand pressing takes a long time, and the more precise it is, the longer it takes. Precision in this step saves our watchmakers a lot of adjustment work later on. Our machine can set the ruby to the correct position, and more importantly, in relation to the correct reference plane on the plate. In addition to speed, this is the great advantage for precision. Here, the automated process serves quality and efficiency, at every step, for every single jewel. The monitoring of the press-in positions and the press-in forces takes place completely automatically during production. Modern technology, put to good use.
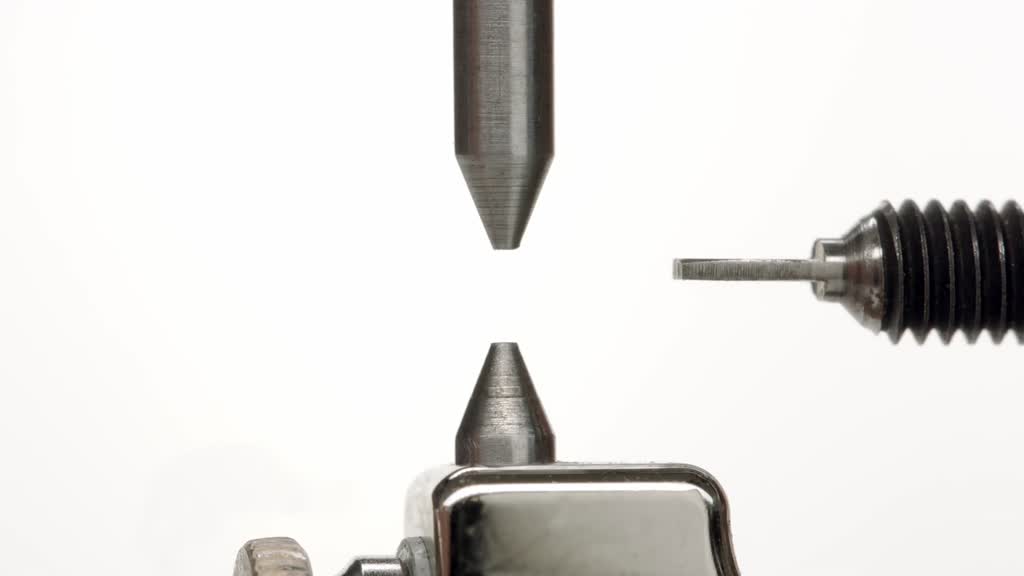
4.2. Freewheeling escape wheel
The escape wheel; an important part of the NOMOS swing system. In order to optimize the interaction of all the elements, our designers spent a great deal of time on calculations, simulations, and tests, only to return to the calculations again. Many rounds were made, because every detail counts. The angles, surface finish, mass, and most importantly, the inertia are all critical factors. Imagine a runner who starts a 100-meter sprint. But shortly after starting they stop again, not even running two meters. Just starting and stopping again. And starting and stopping again. Our escape wheel does this six times a second, or 518,400 times a day. But between the many assembly and control steps, it is simply allowed to spin in this film. Several laps without stopping, almost like a long-distance run—what luck!
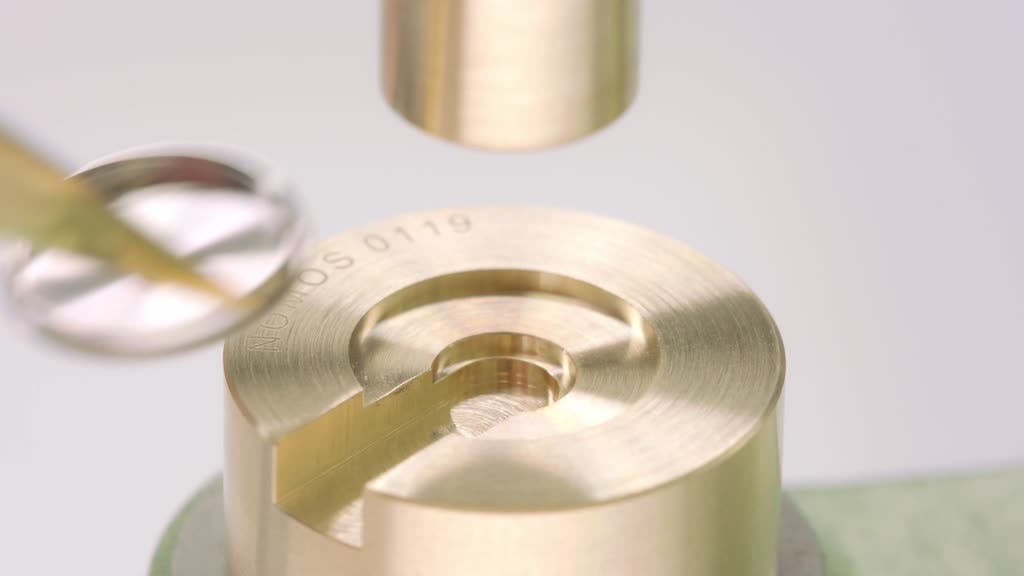
4.1. Inserting the mainspring into the mainspring barrel
A small powerhouse: the mainspring stores the energy supplied and releases it slowly and evenly to the gear train. The film shows the mainspring of our hand-wound movements. A small plate is welded onto the end of the mainspring to anchor it in the barrel. It ensures that the mainspring does not simply slip through. When winding a hand-wound watch, therefore, there is always a noticeable resistance at the end. Fully wound, it won’t move. The situation is different with automatic watches. Since their rotor wants to wind the spring further with each movement, there should be no resistance here when fully wound. The rotor winds relentlessly. In fact, the automatic mainspring needs a sliding fence at the end, which allows it to slip through in a controlled manner. It feels like an automatic watch can be wound infinitely by hand. But regular wear is also enough.