It’s very simple: We have tried to summarize in a few major steps how NOMOS watches are made in Glashütte. It can often take years from when the first drafts are drawn up before the watches are ready for the market, and to be sent out into the world.
1st year, January
The movement is designed—a complicated matter. Forces and tolerances have to be calculated, wheel teeth worked out, plates, bridges, and cocks drawn. Thousands of possibilities are considered, but most are rejected: What functions on paper sometimes doesn’t work in real life. New ideas, new drawings, new dimensions follow. So remember: A good movement has gone through many stages of development before production really begins.
Parallel to the work of draftsmen, toolmakers, and watchmakers in Glashütte, designers in Berlin are busy drawing: The case of the new watch is first created on a computer monitor, or sometimes the old fashioned way—in a sketchbook. The designers ask themselves: What would the new watch be if it were a car, a piece of furniture or jewelry? What does a watch have in common with a well-set diamond? Or with the arena of a football stadium? What frame of mind should the new watch convey? What sort of person would wear this, a whole life long?
Models are built, first from plastic, then from brass. The model enables the designers to check quite precisely: Is the bezel too delicate? Are the case horns too pointed? What is the course of the twist leading to the case? Fractions of millimeters, materials, surfaces: Everything depends on tiny details. The same applies to the dial, which we generally don’t draw until after the case meets our stringent aesthetic demands.
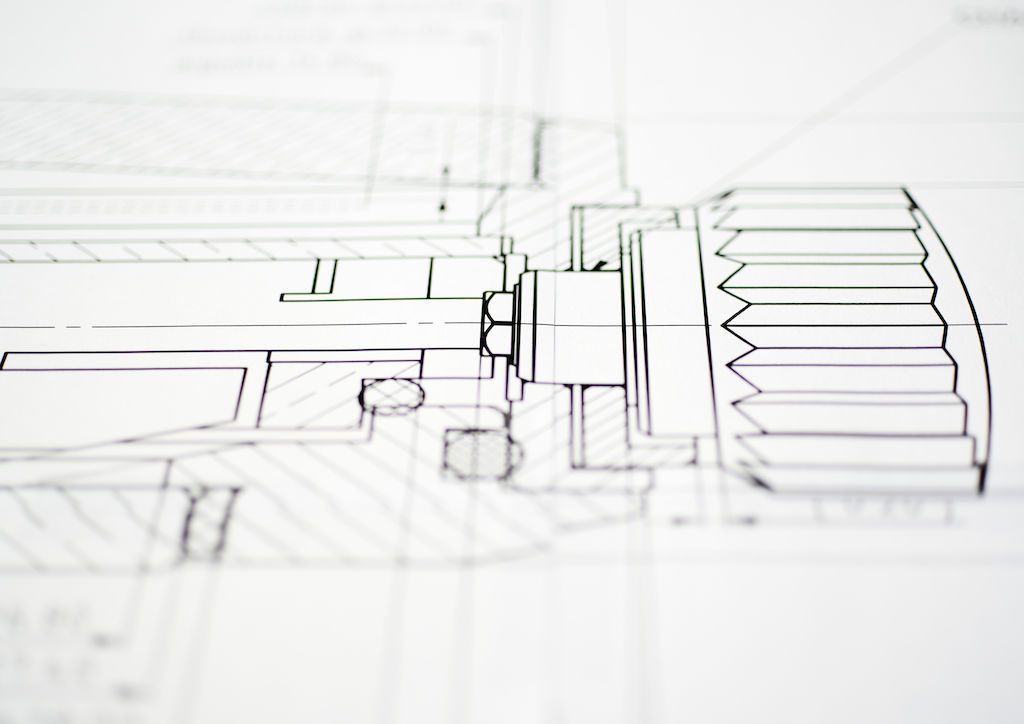
2nd year, January
Models are built in collaboration with specialist dial and case makers; generally speaking, there is often quite a period of back and forth between them, our NOMOS design engineers, and our sales and design staff. When everything is just right, functions properly, and is pleasing to the eye, and when the movement has been decided on and a prototype series is made, orders are placed for raw materials for the plates and bridges; that is, for brass and steel. The metals are die-cut, tempered, relaxed, and ground to tolerances of thousandths of a millimeter—steps that require months. But these are a precondition for the high precision of NOMOS watches.
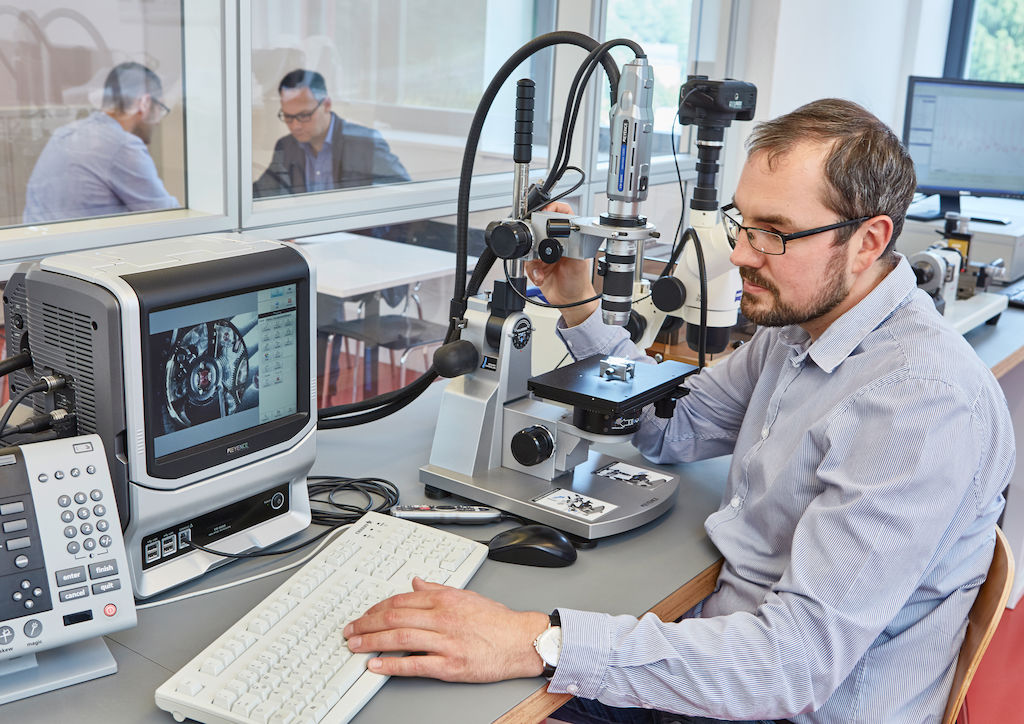
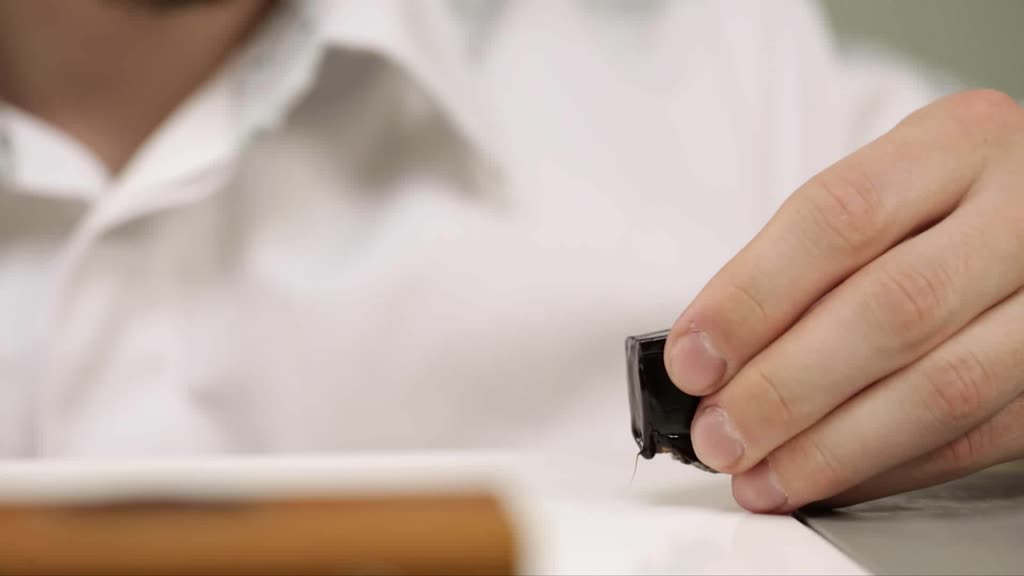
3rd year, July
A great deal of time has already passed, but it was needed. Now, at the start of series production, steel and brass rods three meters in length are produced. From them, the NOMOS toolmakers cut out workpieces to be turned on the lathe to create the pillars, pinions, and bushings for the future caliber. Plates and bridges, but also steel springs are milled, drilled, and eroded. Many parts have to be hardened and given gear teeth, polished and burnished. Only then comes the finishing polish: Glashütte stripes and sunburst decoration denote a caliber’s fine Glashütte provenance. Now we school all our watchmakers in the use of these new tools and parts. Jewels, pins, and pillars form part of the caliber’s frame. Wheels and pinions are pre-mounted. And technical and optical quality controls are carried out again and again.

4th year, January
We’re entering the fourth year since the whole process began: The movement is assembled—and ticks for the first time. Watchmakers now say “it’s alive.” For everyone who wants to know the exact details: Each year from now on, the watch will tick 100 million times and tock 100 million times. The mechanical oscillation of a watch is 3 hertz: that’s six half-swings per second (the escapement halts the watch six times a second) or 518,400 times a day. So the first tick is a big moment that we like to celebrate a little.
After this important step, the caliber—still without the watchcase—is regulated in six positions over a span of seven days. This timing check is so precise that the result is almost as exact as what watches achieve when they go through the chronometer test, which is much more expensive because of its intensity. In all dial and crown positions, the NOMOS watch must achieve the best results in this step. Additional quality controls follow.
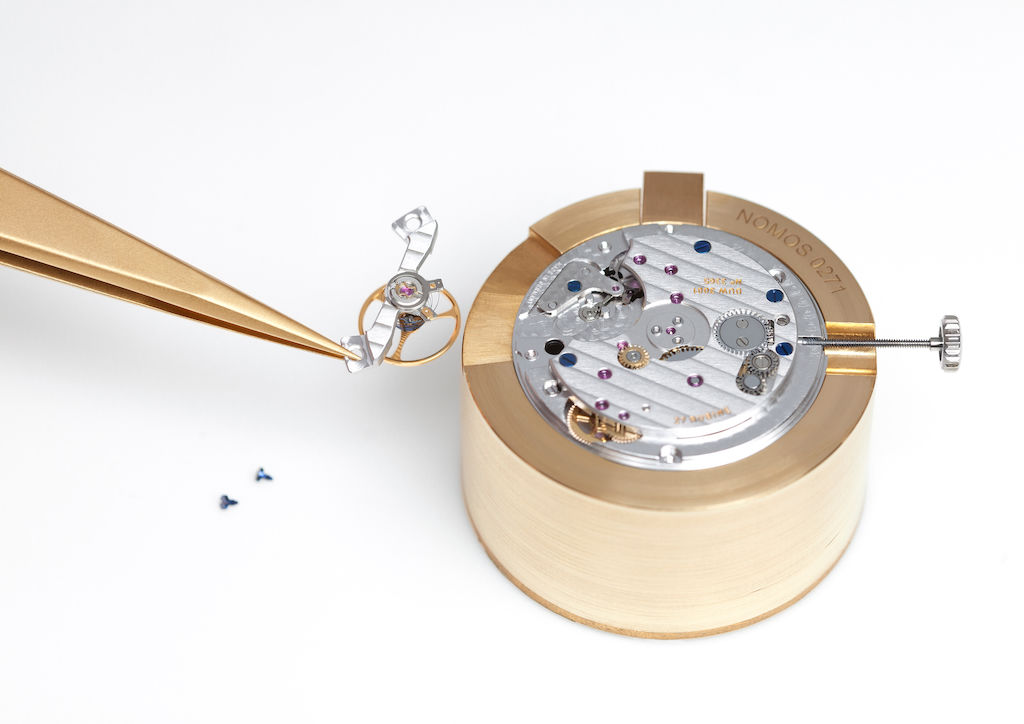
» We go to levels of effort that many would consider extreme. This is why buying a NOMOS watch is an investment in lasting values—in something that stands the test of time. You have my word.« Uwe Ahrendt, NOMOS CEO
4th year, February
In watches with a date function, the date ring is only now set around the caliber and set in motion. This not only decides whether the watch will know what day of the month it is. It also determines whether the watch will have a light or dark face: The color of the date ring determines the color of the dial. Then the watch is equipped with its dial and hands. The caliber is placed into the watchcase, a process called encasing.
The rate of the watch is tested once again: It is placed on the so-called watch winder, which simulates various everyday stresses and strains, and then it must prove its precision again for a week in six positions. Only then is the watchstrap attached—usually one made of Horween Genuine Shell Cordovan; the finest, but also a very robust type of leather. The smaller NOMOS models usually receive a velour leather watchstrap, because its more delicate appearance suits these watches better.
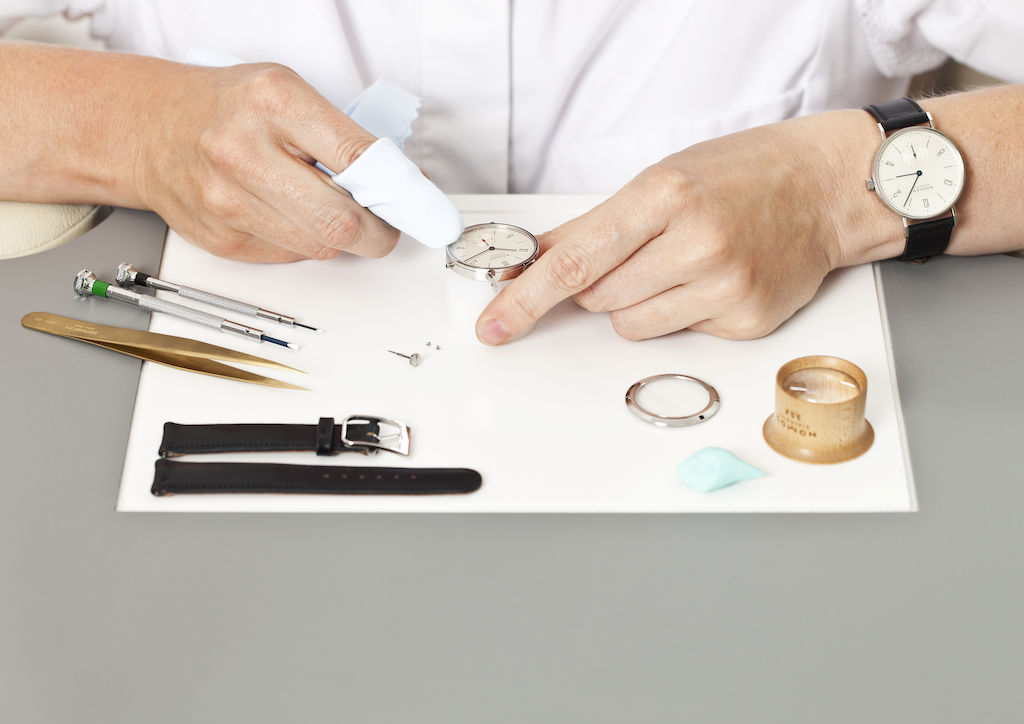
4th year, March.
At the Baselworld trade fair for watches and jewelry in Switzerland, the time has come: The watch is presented to the press and retailers. And shortly afterwards, it is ready to be sent to stores, to travel the world. We’re delighted—and start again from the beginning.
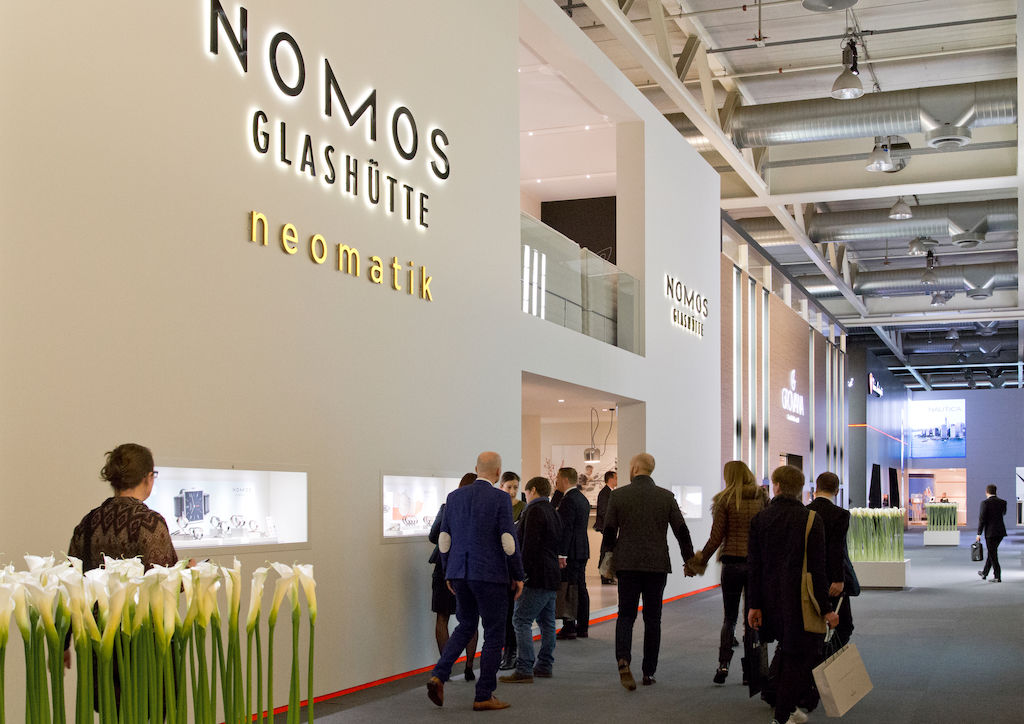