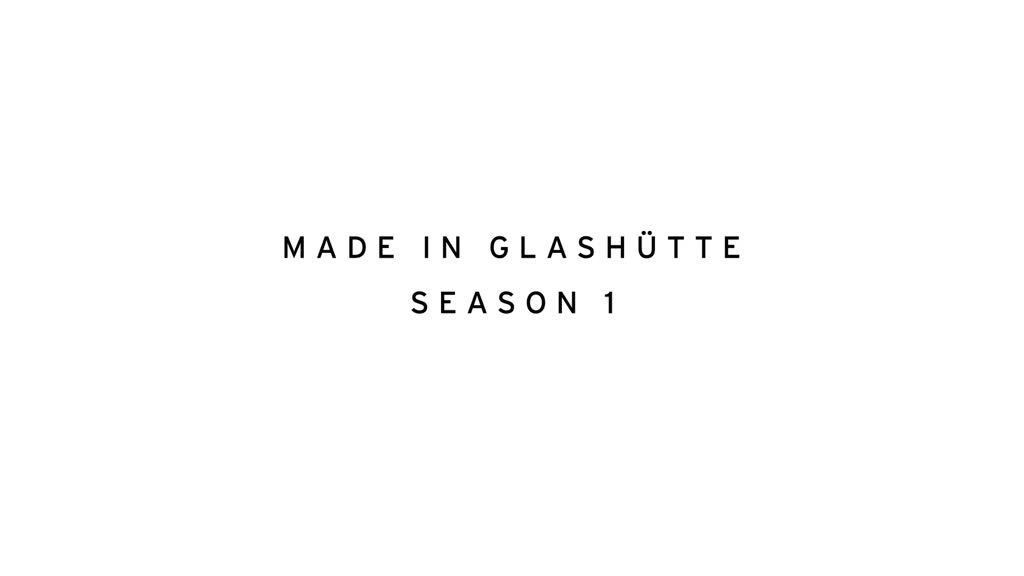
Made in Glashütte : nos processus en détail
« Made in Glashütte » est le titre que nous donnons aux vidéos dans lesquelles nous détaillons les processus de travail dans notre atelier. Chaque étape cruciale de la fabrication d'une montre est clairement visible dans ces séquences du point de vue de nos horlogers et horlogères. Le calme et la concentration avec lesquels nos experts effectuent une multitude d'étapes précises rendent tangibles l'expertise et l'expérience – des qualités que l'on retrouve dans nos montres. Les premières descriptions des différents processus de travail de notre atelier ont été accueillies avec beaucoup d'intérêt par les adeptes des garde-temps. Nous sommes donc ravis de poursuivre. La deuxième saison commencera le 1er janvier 2023 et vous pourrez vous y abonner via nos réseaux habituels. Vous trouverez ci-dessus une compilation de la première saison.
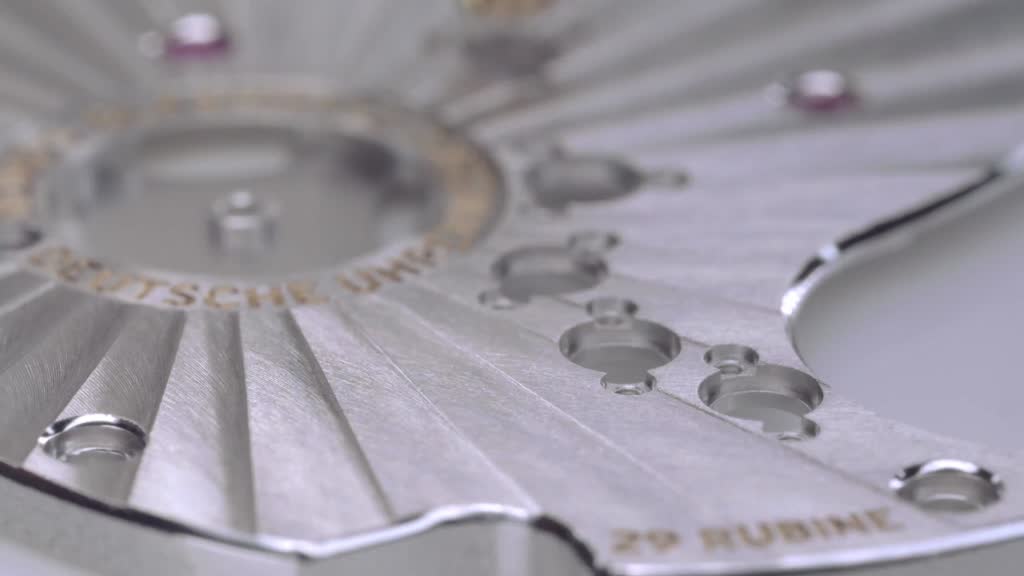
1.12 Insertion des chatons
Rubis fixé dans l'or. Le soin de l'esthétique. Auparavant, ce montage avait l'avantage technique de parfaitement définir et maintenir l'espacement entre les roues. Les portants de rubis pour les pivots des roues n'étaient pas pressés, mais fixés. Une fixation d'or était idéale pour cela ; la malléabilité de ce métal permettait à la pierre d'être parfaitement enchâssée. De plus, la pierre dans son chaton poli développe toute son « incandescence » lorsque le rouge du rubis se reflète dans la cavité du chaton. L'insertion et le vissage des chatons requièrent un geste particulièrement assuré. Les horlogers retiennent même parfois leur souffle, car le polissage devait être recommencé au moindre tremblement. La précision des manufactures modernes évite d'avoir recours à ce procédé. Les pierres peuvent être pressées directement sur les platines. Et qu'en est-il de l'incandescence ? Cette tradition, qui met en valeur les parfaites interactions entre couleur et lumière, mais aussi entre taille et polissage, perdure sur nos montres les plus raffinées.
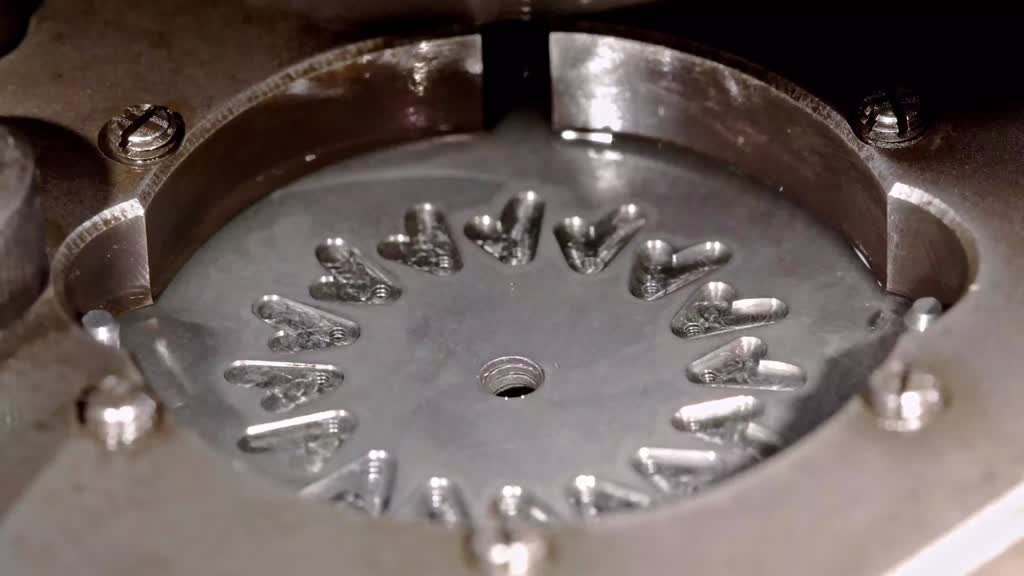
1.11 Usinage par électrode-outil
Connu sous le terme « d'étincelage », ce procédé envoie des étincelles via un filament pour couper les plus petits des éléments d'un disque avec une extrême précision. La machine peut fileter le filament dans la pièce à usiner et commencer à la tailler sous l'eau (eau ionisée ou diélectrique). L'intérêt est que plusieurs disques peuvent être usinés simultanément et produire plusieurs éléments en parallèle, ce qui est difficile à obtenir avec une scie à chantourner.
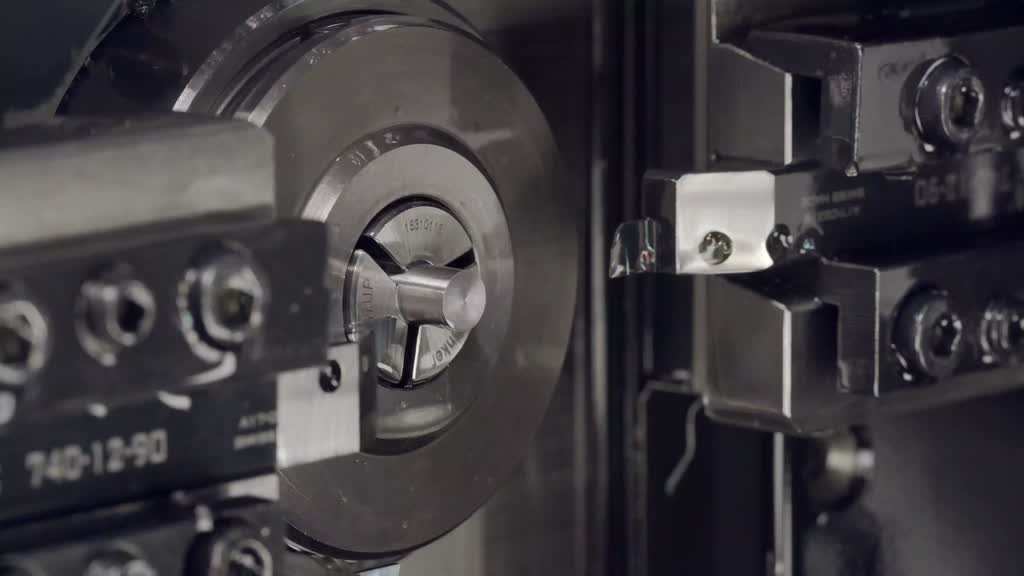
1.10 Tournage de la roue du correcteur
De nombreuses opérations sont requises pour produire la roue du correcteur. Tournage, centrage, perçage, contrefraisure, ébarbage… tout ceci est possible sur notre tour CNC automatique. Mais la machine ne fait que suivre les instructions de nos programmeurs. Et tout cela implique de nombreux réglages. Vitesse, déplacements, alimentation, sélection de l'outil adapté, et quantité et température parfaites de l'huile de coupe. Et n'oublions pas les outilleurs. Après tout, la qualité n'est au rendez-vous que grâce à la perfection du travail des spécialistes derrière les machines.
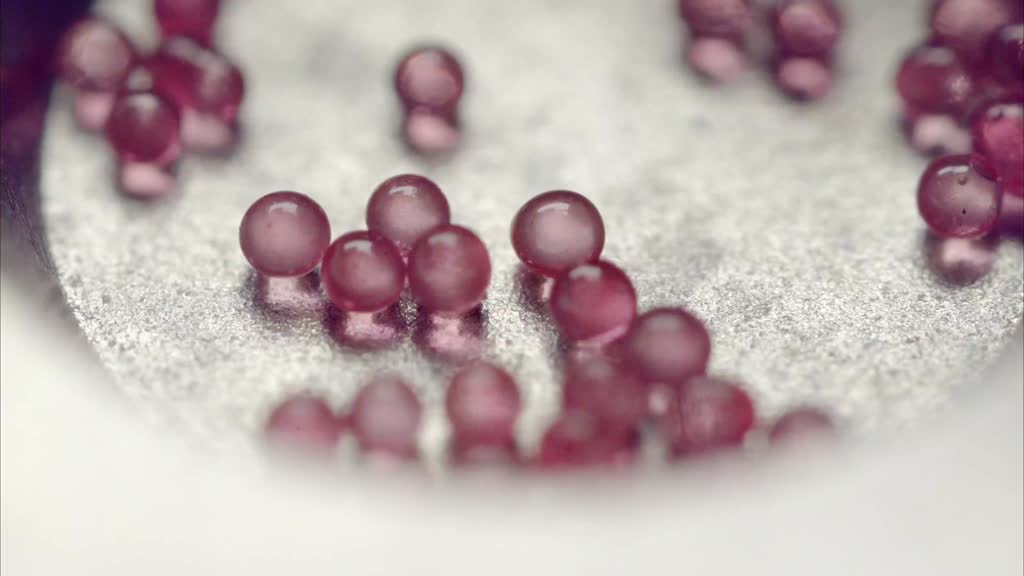
1.9 Fixation de l'échappement
De petites perles roses d'adhésif créent un lien ferme à basse tension entre le balancier et le pont de balancier. Plus précisément, la terminaison du spiral est collée au tenon. Auparavant, le spiral était inséré dans un trou avec une goupille, ce qui créait de la tension et des déformations. Assurer à la fois précision et stabilité rendait cette étape très chronophage. La technique de fixation permet une connexion délestée de toute tension entre le système de balancier du coq et le pont de balancier. Le spiral et le coq peuvent immédiatement commencer leur travail de cadence de la montre avec une précision constante. Chaque perle d'adhésif a un diamètre de 0,35 mm et un volume de 0,025 mm³, pesant 0,029 mg. Avec un demi-litre de perles adhésives, nous pourrions fixer plus de 15 millions de spiraux.
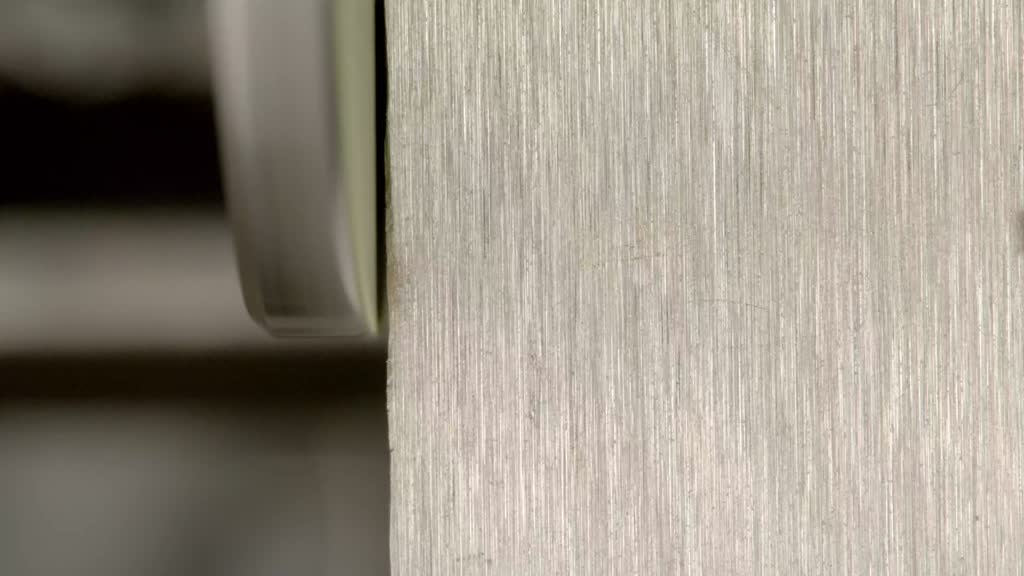
1.8 Meulage de la bavure de maintien
Les technologies modernes sont capables de réaliser beaucoup de choses, et surtout de réaliser beaucoup de choses à la fois ! Néanmoins, elles ont toujours leurs limites. Le fraisage et l'usinage par électroérosion des diverses pièces qui composent le blanc-roulant requièrent ensuite de meuler la bavure que laissent ces opérations. Sans cela, les pièces finiraient par être délogées et qui sait où elles finiraient à l'intérieur de la machine. Dans tous les cas, une telle excursion signerait l'arrêt de mort de la pièce en question. De ce fait, nous préférons donc meuler la bavure qui maintient les pièces en place jusqu'à la dernière étape d'usinage. Avec beaucoup de pratique, cette opération s'effectue très vite et très précisément.
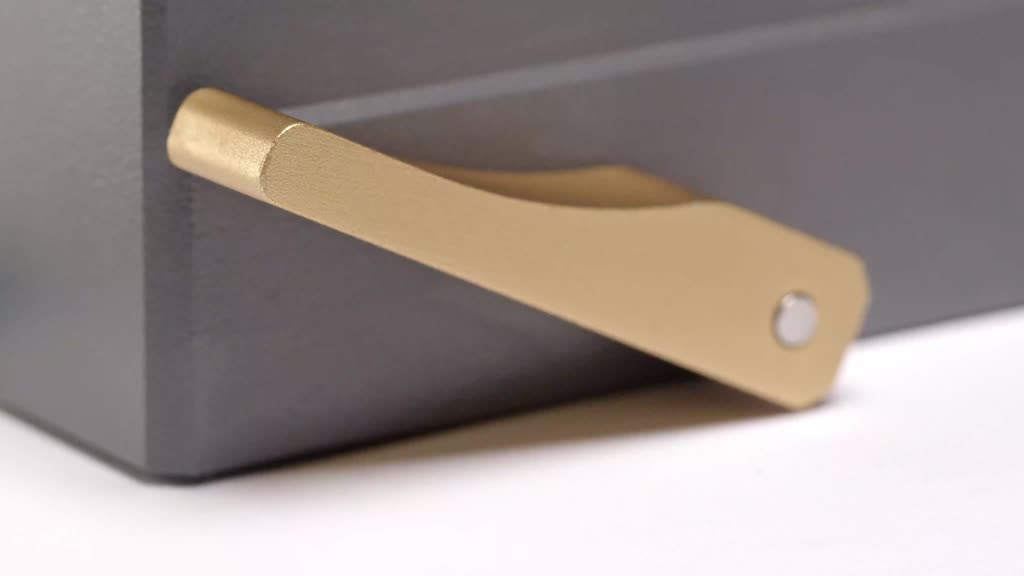
1.7 Mesure de la profondeur de fraisage
Le contrôle est constant de la première à la dernière trace de fraisage. L'élément final fonctionnera avec la fiabilité requise seulement si chaque étape du processus est réalisée avec succès. Et ici, le contrôle qualité doit être appris. La bonne technique de mesure doit être employée pour des résultats exécutables. Et si tout correspond lors de la vérification, cette trace de fraisage deviendra un capot de levier de date.
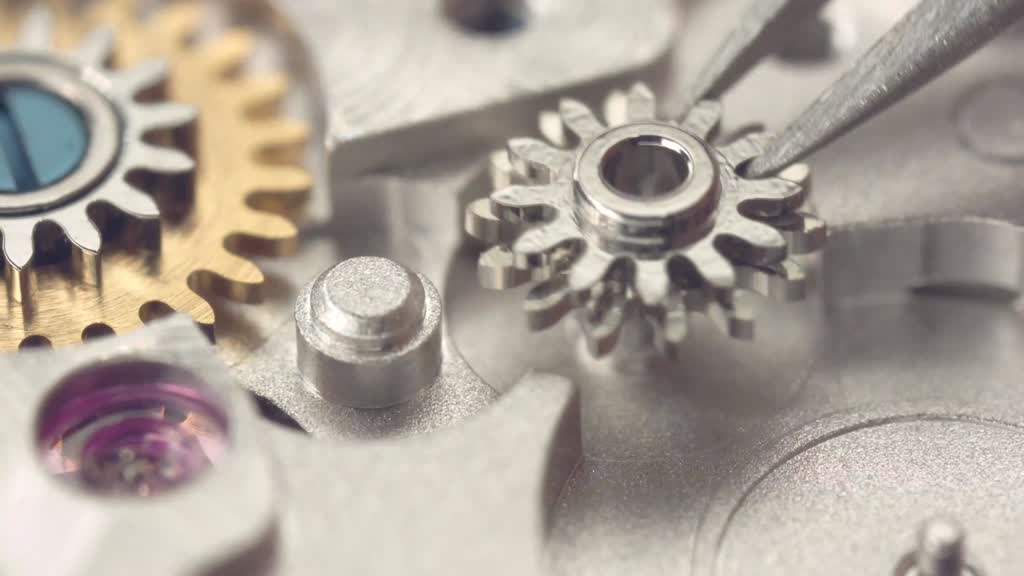
1.6 Assemblage du mécanisme de date
Le mécanisme de date breveté dans notre calibre DUW 6101. La fonctionnalité phare repose sur le disque programme en forme de cœur qui fait que notre cliquet entraîne l'avancement de la date une fois toutes les quatre révolutions. Pas de grande roue de 24 heures. Une solution constructive qui requiert peu d'espace et qui nous permet de produire des mouvements très plats. Cependant, pendant l'assemblage, une attention particulière doit être portée au positionnement de tous les éléments par rapport aux autres. Si nous y parvenons, alors tout roulera pour le mieux.
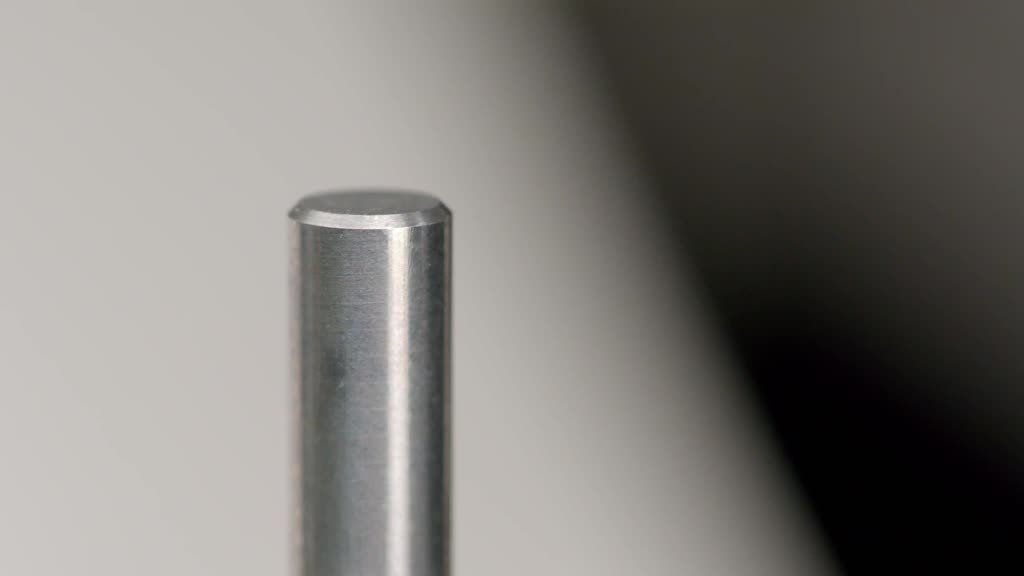
1.5 Outils de polissage
Pour obtenir un bon résultat, il faut de bons outils. Dans l’optique d’assurer une excellente qualité, nous fabriquons nous-mêmes nos outils. Les avantages sont nombreux : plus de créativité dans le processus de construction, nous permettant de façonner des contours et des formes plus complexes que ce qu’un outil standard pourrait accomplir. Lors de la fabrication, nous pouvons peaufiner les processus d’usinage pour réaliser notre vision et donner au matériau les propriétés souhaitées, rehaussant encore plus la qualité et la productivité. Nous sommes flexibles et rapides, et gagnons en expérience chaque jour. Comme toujours à Glashütte, nous optimisons chaque aspect de notre travail.
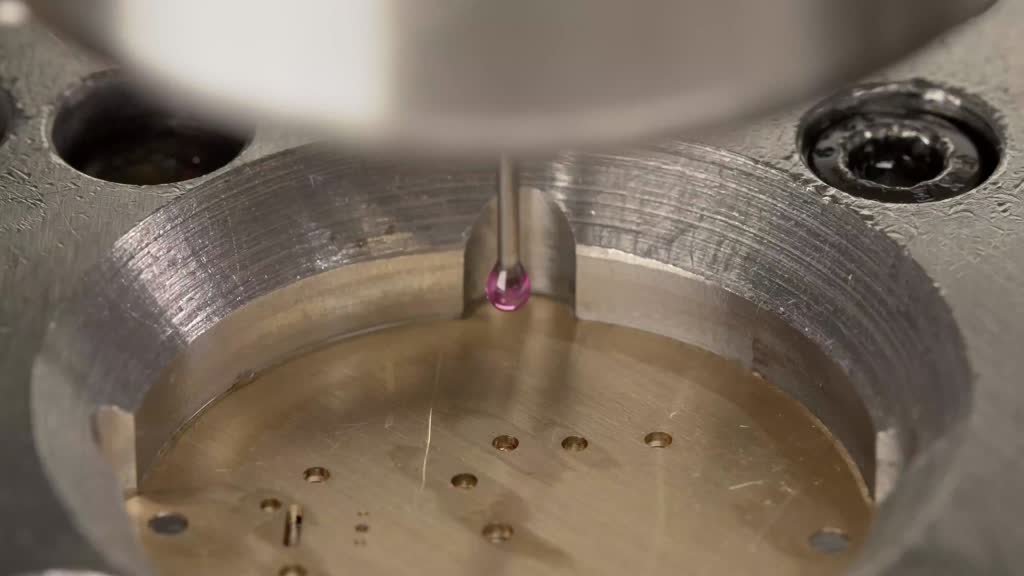
1.4 Fraisage de la platine trois-quarts
Avant de fraiser, il convient de mesurer. Il est essentiel que le blanc roulant ait la bonne épaisseur et la bonne position dans la machine. Après tout, il est ici question d'une précision de l'ordre du micromètre (mµ). Chaque point de départ, chaque mouvement de la fraiseuse, la chronologie des contours, des plans et des perçages... Rien de tout cela n'est laissé au hasard, bien au contraire : tout est prédéfini avec une précision certaine, fruit d'une longue expérience. De nombreux outils sont échangeables automatiquement pour garantir en permanence une qualité et une efficacité optimales. La vitesse de rotation et d'avancée de la fraiseuse sont coordonnées rigoureusement pour éviter un ébavurage manuel fastidieux, stigmate d'un fraisage précipité. Pas de ça chez nous. Ici, la qualité est un gain de temps, d'autant que nous aimons réduire chaque chose à l'essentiel ! Le fraisage du blanc roulant est à l'image de la future montre : tout en précision.
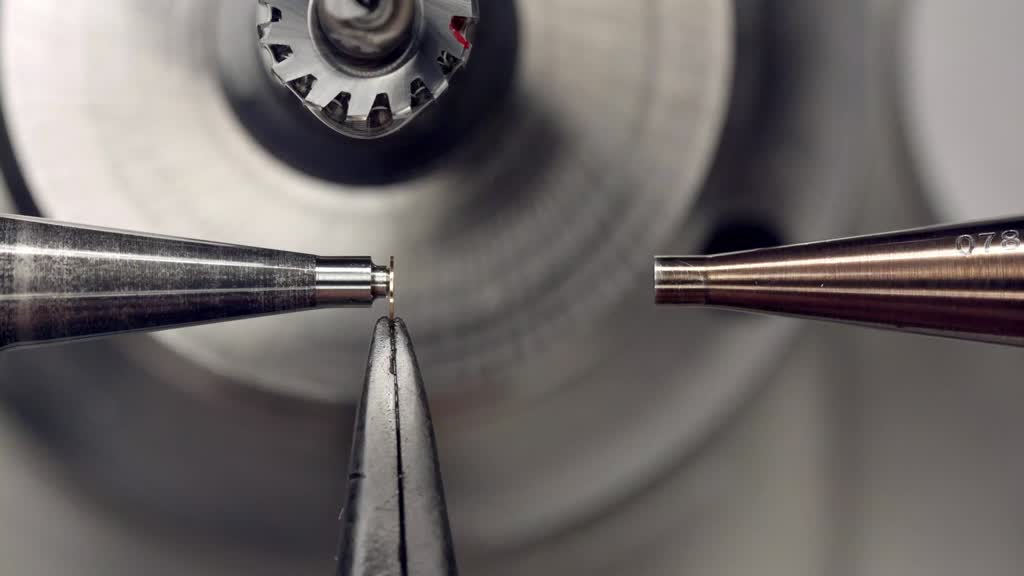
1.3 Taillage par génération des engrenages de la roue d'accélération
Le processus de taillage par génération des engrenages garantit l'absolue symétrie des dents. Ici, toutes les dents sont usinées au même moment. Auparavant, tous les vides entre les dents étaient fraisés successivement dans autant de sous-séquences. Cela assurait que les vides étaient similaires et bien taillés, mais le résultat n'était pas toujours parfaitement fonctionnel. Cependant, la production de fraises à tailler appropriées, mais aussi le réglage ultra précis des machines, sont devenus de véritables défis de nos jours. Grâce à nos tourneurs fraiseurs spécialistes du taillage par génération, les dents de chez NOMOS Glashütte ne sont pas juste similaires, elles sont parfaitement identiques !
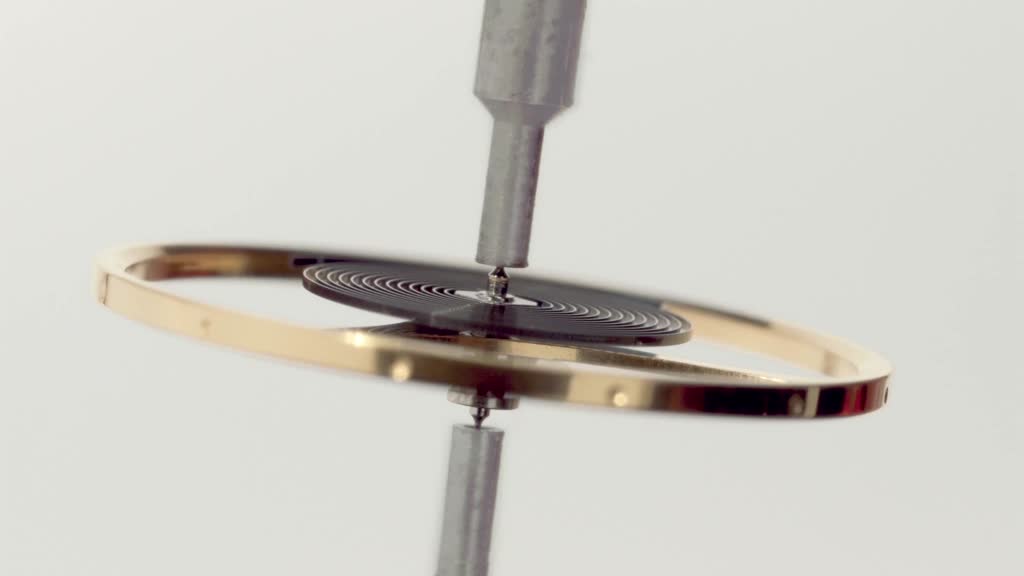
1.2 Ajuster le spiral dans la montre
Une fois notre spiral bleui NOMOS associé au pont de balancier sélectionné, il doit être à nouveau minutieusement examiné. Un horloger doit vérifier que tout tourne rond et de manière régulière. Dans le cas contraire, mieux vaut agir maintenant, car toute correction ultérieure sera quasiment impossible. Seul un petit nombre d'experts peut identifier et rectifier ces problèmes. Des mois de formation sont nécessaires pour être capable de réaliser ce travail. Nos ingénieurs ont développé des logiciels de formation qui entraînent l'œil à reconnaître ces défauts. Dans une montre NOMOS, le spiral se doit d'être parfait.
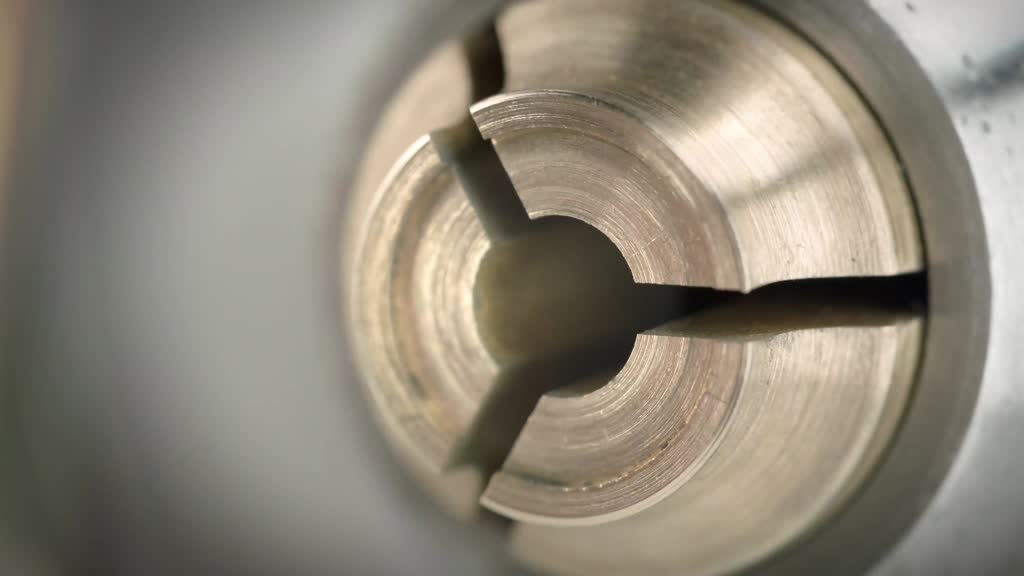
1.1 Polissage en soleillage de Glashütte
Une décoration aussi traditionnelle que sa conception. Un polissage en soleillage de Glashütte inimitable, aussi bien à l'époque de Ferdinand Adolph Lange qu'aujourd'hui chez NOMOS. Il existe bien des polissages comparables. Tous sont le produit d'outils variés. Papier de verre, cutter, brosse en acier... mais l'aspect rayonnant du polissage en soleillage de Glashütte peut uniquement s'obtenir grâce à une meuleuse stylo accompagnée d'une pâte à meuler adéquate. Quel genre de stylo ? C'est un secret ! Quel genre de pâte à meuler ? Alors ça, c'est encore plus secret ! Des centaines de tests ont été effectués pour perfectionner le mouvement de meulage, et la recette de la pâte à meuler a fait l'objet d'innombrables modifications au fil du temps. Et ici aussi, il faut faire appel à des employés chevronnés pour peindre le soleil sur la meule. Un secret à lui seul ne suffit pas.