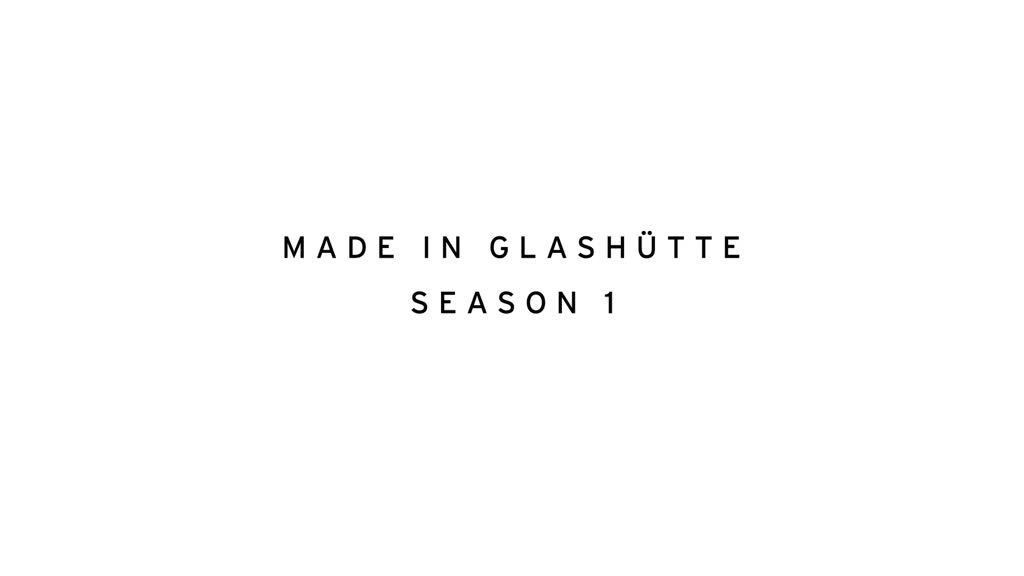
Made in Glashütte: trabajo retratado
«Hecho en Glashütte» es el título que le damos a las secuencias cinematográficas en profundidad en las que retratamos los procesos de trabajo en nuestra fábrica. Los pasos individuales que son importantes en la fabricación de cada reloj son claramente visibles en estas películas desde la perspectiva de nuestros relojeros y relojeras. La calma y la concentración con la que los expertos llevan a cabo una multitud de pasos precisos hacen que la habilidad y la experiencia resulten tangibles: las mismas cualidades que se pueden encontrar en nuestros relojes. Los entusiastas de los relojes han recibido con gran interés los primeros retratos de los pasos de trabajo individuales de nuestra fábrica. Por eso, estamos motivados para continuar. La segunda temporada comenzará el 1 de enero de 2023 y puede suscribirse en los canales habituales. Más arriba encontrará una recopilación de la primera temporada.
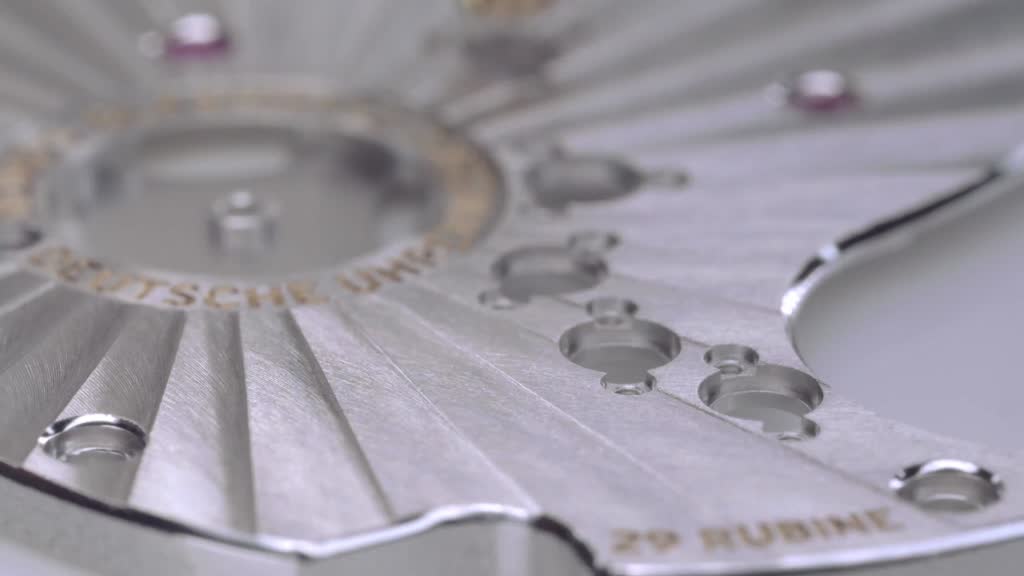
1.12 Inserción de los chatones
El rubí engastado en oro: un placer estético. En el pasado, esto también tenía beneficios técnicos: definir y mantener perfectamente la separación de las ruedas. Los cojinetes del rubí para los pivotes de las ruedas se engastaban, no se prensaban. Una montura en oro era ideal para esto, dado que el material es suave y permite que la piedra se engaste bien. Además, la piedra del chatón pulido desarrolla su «fuego» cuando el rubí rojo se refleja en el hueco del chatón. Se necesita una mano particularmente estable para insertar y atornillar los chatones. Los relojeros a veces incluso contenían la respiración, ya que el mínimo temblor podía suponer el comienzo del pulido desde el principio. Las precisiones de la fabricación moderna ya no requieren engaste. Las piedras se pueden prensar directamente en las placas. Pero, ¿y qué pasa con el fuego? Esta tradición y la perfecta interacción del color y de la luz, del corte y del pulido, perduran en nuestros excelentes relojes.
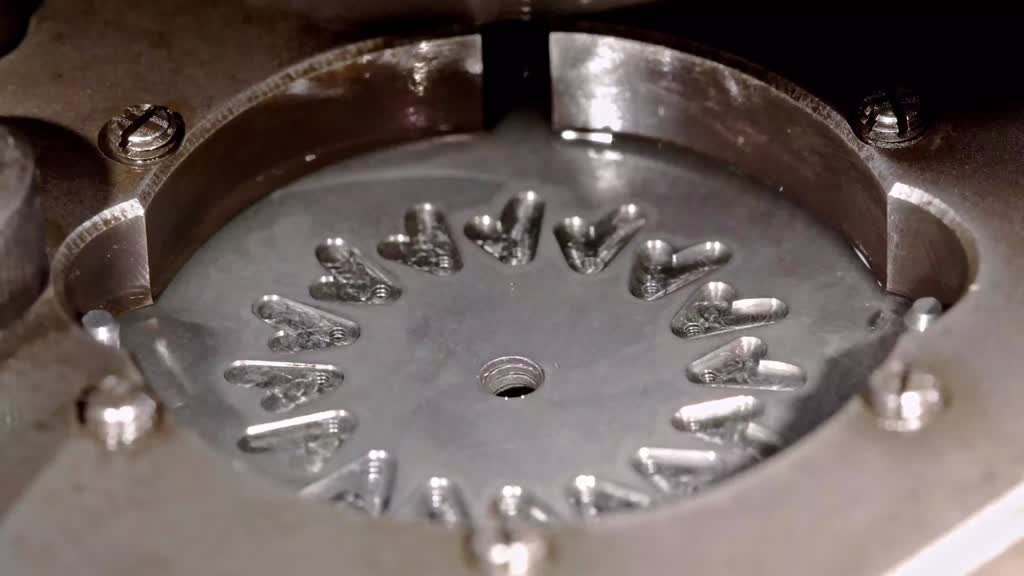
1.11 Mecanizado por descarga eléctrica
Coloquialmente denominado «mecanizado por chispas», un alambre usa las chispas para cortar los componentes más pequeños con la extrema precisión de un disco. La máquina puede ensartar el alambre en la pieza y luego comenzar a cortarla bajo el agua (agua ionizada o fluido dieléctrico). Lo maravilloso es que se pueden mecanizar varios discos a la vez, por lo que se pueden producir varias piezas de una sola vez, algo que resulta difícil con una segueta.
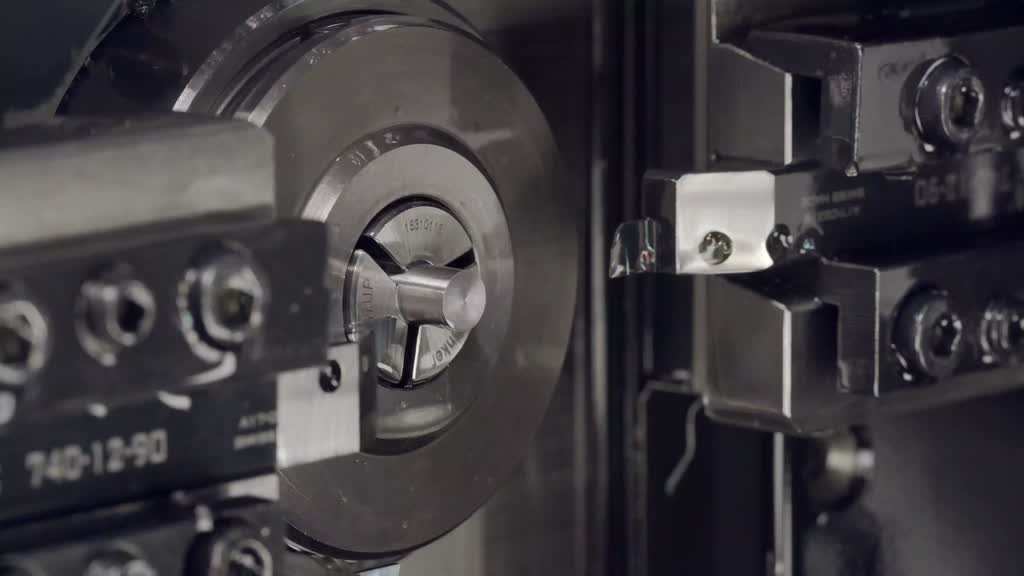
1.10 Giro de la rueda correctora
Se requieren numerosas operaciones para producir la rueda correctora. Girar, centrar, taladrar, avellanar, desbarbar... Todo ello es posible en nuestro torno CNC automático. Pero la máquina solo hace lo que nuestros programadores le ordenan. Y eso conlleva numerosos ajustes. Velocidad, desplazamientos, alimentación, la selección de la herramienta correcta y la cantidad y la temperatura perfectas del aceite de corte. Y no nos olvidemos de los fabricantes de herramientas. Al fin y al cabo, la calidad es tan buena gracias al trabajo perfecto de los especialistas que controlan las máquinas.
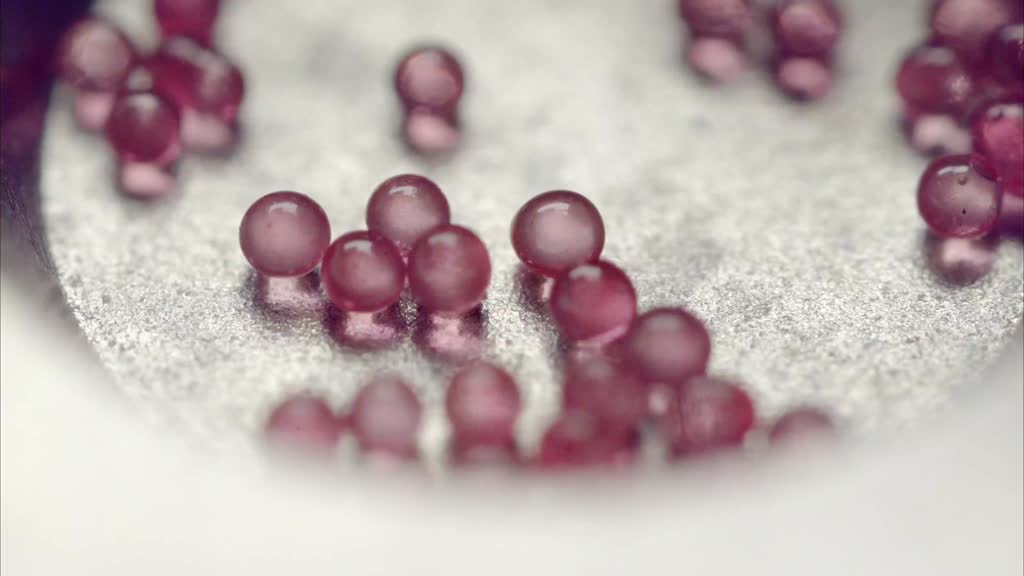
1.9 Unión del escape
Unas pequeñas gotas rosas de adhesivo crean una unión firme y de baja tensión entre el volante y el puente del volante. Para ser más precisos, el extremo de la espiral del volante se pega a la clavija. Antes, la espiral se comprimía junto con una clavija en un orificio, lo que generaba tensión y deformación. Se necesitaba mucho tiempo para garantizar una precisión estable. La técnica de unión proporciona una conexión sin tensión entre el sistema de escape del coq del volante y el puente del volante. La espiral y el coq del volante pueden comenzar su trabajo como elemento que marca la marcha del reloj de inmediato y con una precisión constante. Cada gota de adhesivo tiene un diámetro de 0,35 mm y un volumen de 0,025 mm³, con un peso de 0,029 mg. Con una botella de medio litro de gotas de adhesivo, podríamos unir más de 15 millones de espirales.
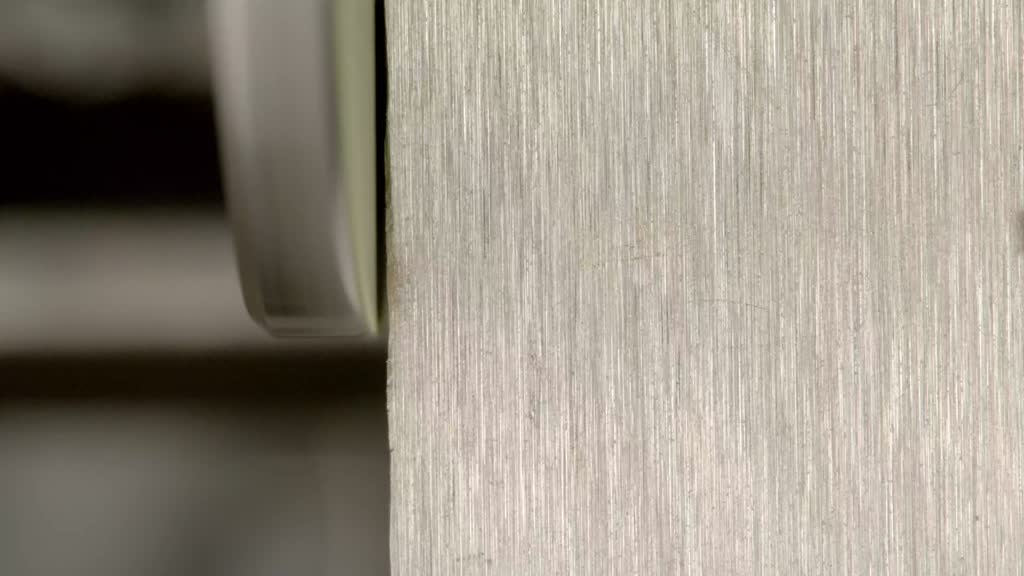
1.8 Desbaste de la rebaba de soporte
La tecnología moderna puede lograr muchas cosas, ¡sobre todo de una vez! Sin embargo, tiene sus límites. El fresado y el mecanizado por descarga eléctrica de múltiples partes de una platina circular en bruto requieren el desbaste posterior de la rebaba de soporte. Si no lo hiciéramos, las distintas partes se desprenderían de la pieza en bruto, y quién sabe adónde irían a parar en la máquina. En todo caso, dicha excursión supondría la pérdida de cualquier parte. Por eso, preferimos desbastar la rebaba de soporte, que mantiene las partes en su sitio hasta el paso final del mecanizado. Con mucha práctica, eso se puede hacer de manera muy rápida y precisa.
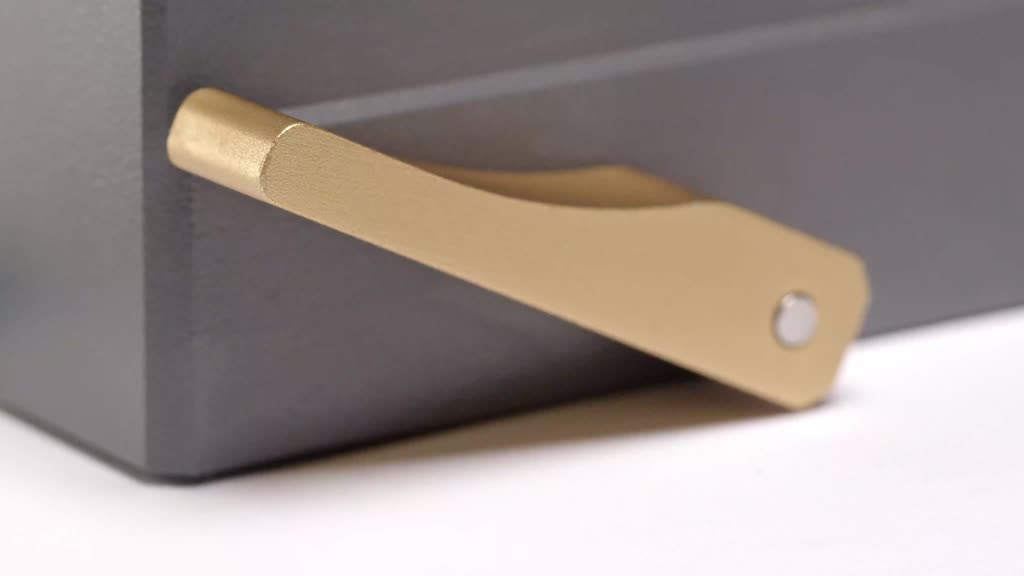
1.7 Medición de la profundidad de fresado
Control constante desde el primer recorrido de fresado hasta el último. Solo cuando cada paso del proceso se ejecuta correctamente el resultado final será un componente que funcione de manera fiable. Y aquí, la comprobación es algo que se debe aprender. La técnica de medición correcta es un requisito para lograr resultados viables. Y si todo encaja, este único recorrido de fresado más tarde se convertirá en una cubierta de palanca de fecha.
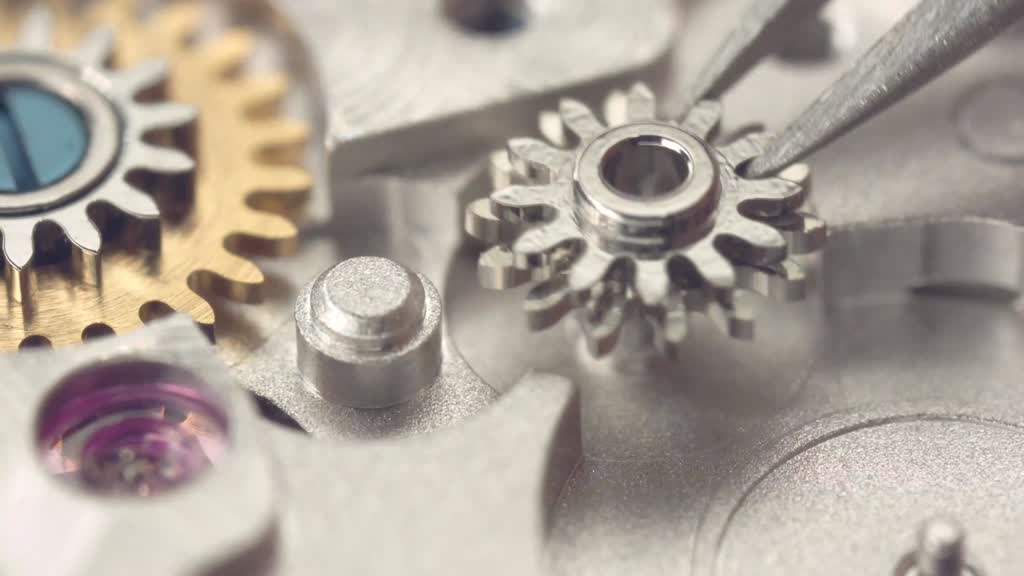
1.6 Montaje de la fecha
El mecanismo de fecha patentado en nuestro calibre DUW 6101. La característica esencial es el disco de programación con forma de corazón que hace que nuestro trinquete adelante la fecha solo cada cuatro revoluciones. Sin rueda grande de 24 horas. Una solución constructiva que requiere poco espacio y nos permite producir movimientos muy planos. No obstante, durante el montaje, se debe prestar especial atención al correcto posicionamiento de las piezas respecto de las demás. Solo si hacemos esto correctamente aparecerá el día siguiente.
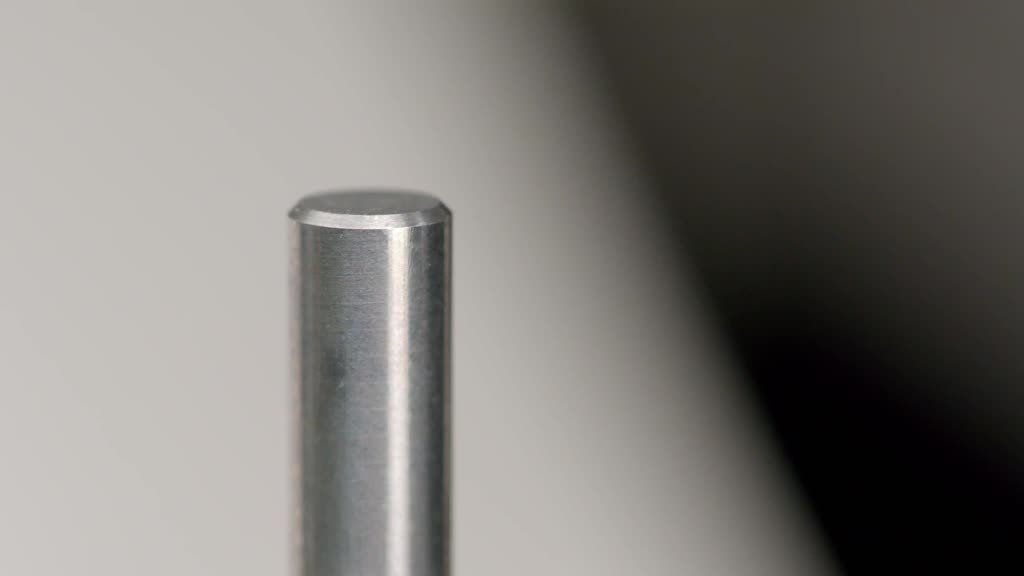
1.5 Herramientas de rectificado
Un buen resultado no es posible sin unas buenas herramientas. Para garantizar una buena calidad, hacemos nuestras propias herramientas, lo que presenta numerosas ventajas: se permite más creatividad en nuestros procesos de construcción y podemos crear contornos y formas que son más difíciles de realizar con herramientas estandarizadas. En la fabricación, podemos ajustar los procesos de mecanizado para que se adapten a nuestras necesidades y a las propiedades del material, lo que proporciona una mayor calidad y productividad. Somos flexibles y rápidos y cada día adquirimos más experiencia. Como es costumbre en Glashütte, optimizamos constantemente lo que hacemos.
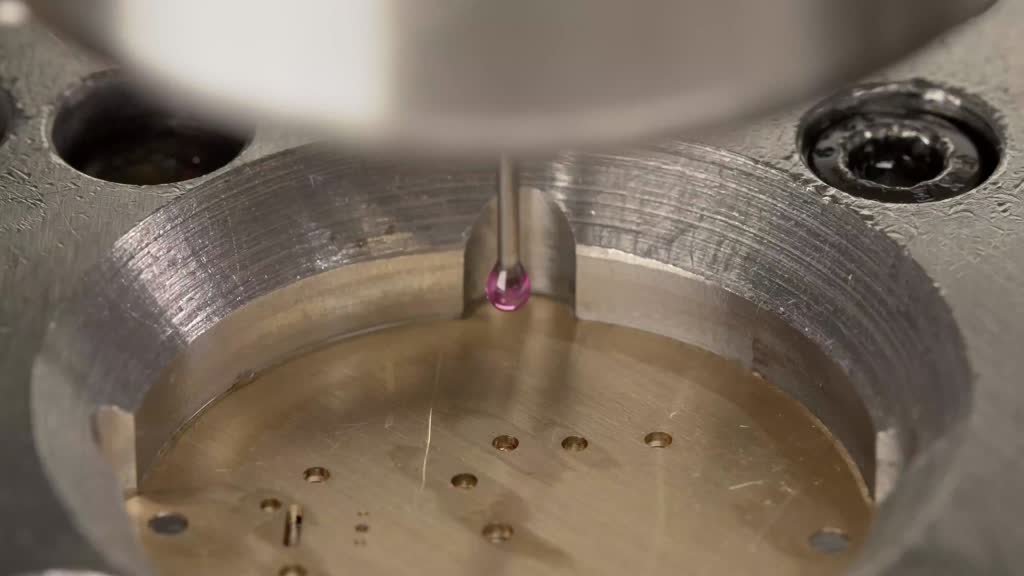
1.4 Fresado de la platina de tres cuartos
Antes de fresar hay que medir. Es de extrema importancia que la platina circular en bruto tenga el grosor correcto y la posición correcta en la máquina. Al fin y al cabo, hablamos de una precisión que va hasta el micrómetro (mµ). Cada punto de partida, cada movimiento de la fresadora, la cronología de los contornos, los planos y las perforaciones... Nada es aleatorio. Todo se ha definido previamente con precisión, recurriendo a una gran experiencia. Muchas herramientas se pueden intercambiar automáticamente para garantizar una alta calidad y una eficiencia constantes. El índice de rotación y la velocidad de avance de la fresadora se coordinan parar lograr un fresado óptimo. Si se fresa demasiado rápido después habrá que dedicar más tiempo a desbarbar a mano. Esto se puede evitar. Aquí, la calidad ahorra tiempo, ¡y nos gusta reducir las cosas a lo esencial! El fresado de las platinas circulares en bruto constituye la base de la precisión del reloj.
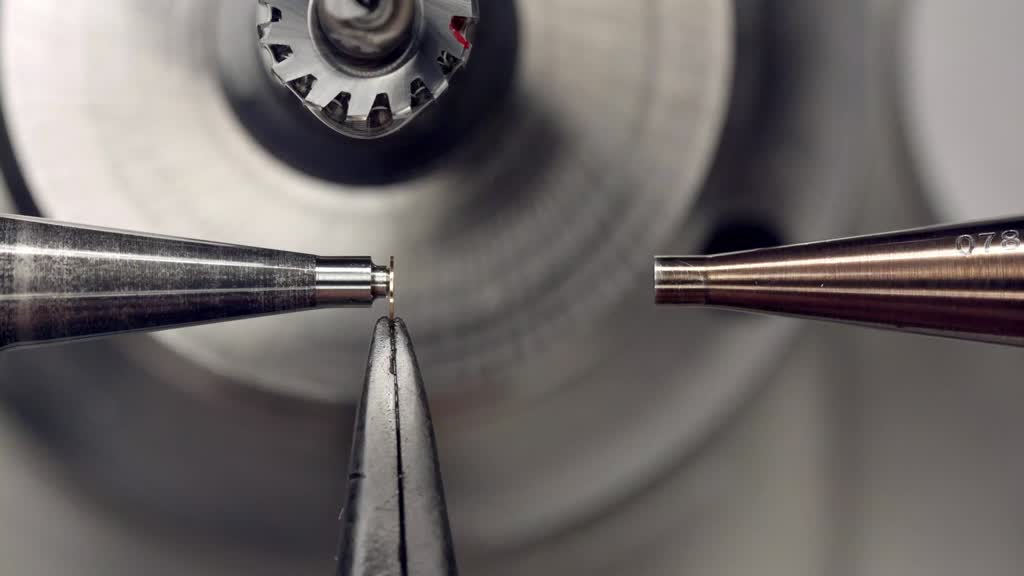
1.3 Fresado de los engranajes de la rueda aceleradora
El proceso de fresado de los engranajes garantiza que todos los dientes sean iguales. Aquí todos los dientes se elaboran a la vez. Anteriormente, el espacio de cada diente individual se fresaba uno tras otro en distintos subprocesos. Esto garantizaba que los espacios entre los dientes eran iguales y armónicos, pero no siempre del todo funcionales. Sin embargo, actualmente la producción de los fresadores adecuados y el ajuste preciso de la máquina supone un reto particular. Con nuestros especialistas fresadores de NOMOS Glashütte, los dientes no solo son iguales, sino también perfectos.
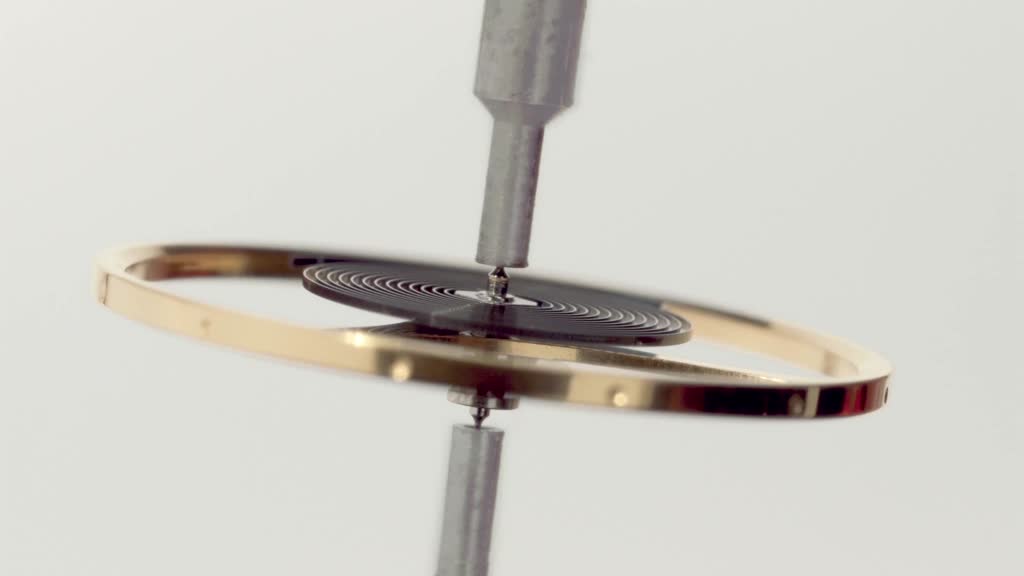
1.2 Ajuste del resorte regulador del reloj
Una vez que nuestro resorte regulador azul templado de NOMOS se ha unido con un puente del volante seleccionado, debe analizarse de nuevo. El relojero comprueba que todo funciona correctamente y manera uniforme. De no ser así, es el momento de actuar o después no se podrá corregir. Solo unos pocos expertos pueden identificar y rectificar estos problemas. Se requieren muchas semanas y meses de formación para poder llevar a cabo este trabajo. Nuestros ingenieros han desarrollado un software para fines formativos que entrena el ojo para que reconozca estos efectos. En un reloj NOMOS solo tiene cabida un resorte regulador perfecto.
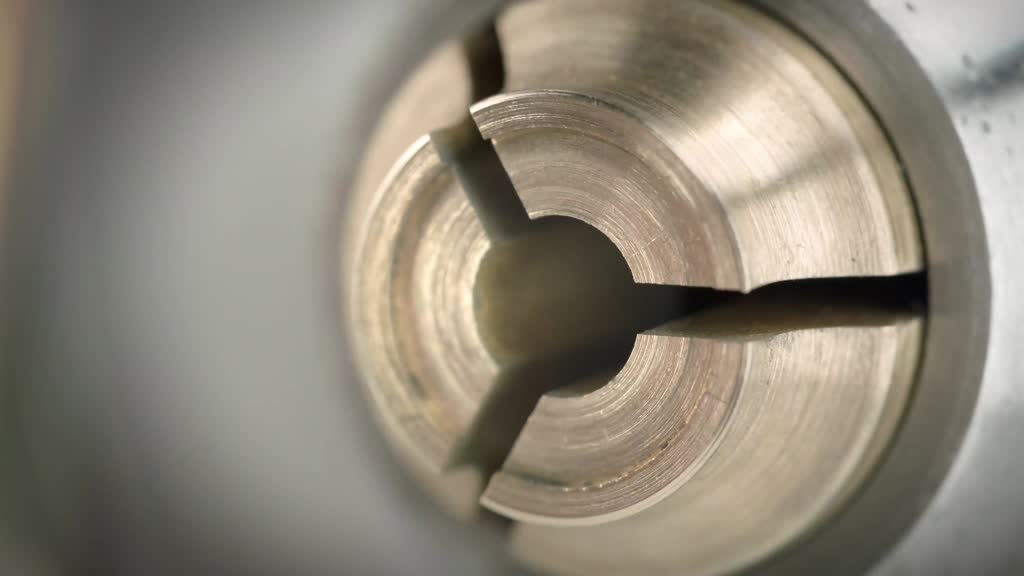
1.1 Pulido radial de Glashütte
Una decoración muy tradicional en un diseño muy tradicional. El pulido radial de Glashütte es inconfundible; hoy en NOMOS tal y como era en la época de Ferdinand Adolph Lange. Hay numerosos pulidos similares. Realizados con las herramientas más variadas. Lija, cuchillas, escobillas de acero... Pero el aspecto radiante del pulido radial de Glashütte solo se puede lograr con un lápiz pulidor y la pasta de pulido adecuada. ¿Qué tipo de lápiz? ¡Es secreto! ¿Qué tipo de pasta de pulido? ¡También es secreto! Se realizaron cientos de pruebas para lograr un patrón de pulido perfecto y la receta de la pasta de pulido se ajustó en innumerables ocasiones. Y también se necesitan empleados muy experimentados para que el sol brille en la rueda. Un secreto solo no es suficiente.